Adampower
NEMA8 Stepper Lead Screw Linear Actuators
The NEMA 6 is our smallest hybrid linear actuators.
This compact unit can be integrated into various
Applications to provide precise linear positioning while
occupying less than 1 in2 of mounting footprint and
providing up to 44.5N of continuous thrust.
The Working Type for the Different Application Demand:
E: External Linear
N: Non-captive
C: Captive
K: Kaptive
Motor Characteristics:
Motor Code | Voltage (V) | Current (A) | Resistance (Ω) | Inductance (mH) | Weight (g) | Lead Wire No | Length (mm) |
8-2105 | 2.5 | 0.5 | 5.1 | 1.5 | 51 | 4 | 27.2 |
8-2205 | 4.4 | 0.5 | 8.8 | 2.7 | 74 | 4 | 38.1 |
Lead Code | Screw Dia. (inch) | Screw Dia. (mm) | Lead (inch) | Lead (mm) | Travel Per Step @ 1.8 deg (mm) |
AF | 0.138 | 3.5 | 0.012 | 0.3048 | 0.0015 |
AA | 0.138 | 3.5 | 0.024 | 0.6096 | 0.003 |
B | 0.138 | 3.5 | 0.048 | 1.2192 | 0.0061 |
G | 0.138 | 3.5 | 0.079 | 2 | 0.01 |
M | 0.138 | 3.5 | 0.158 | 4 | 0.02 |
T | 0.138 | 3.5 | 0.315 | 8 | 0.04 |
NEMA 8 Stepper Lead Screw Linear Actuators (External Type):
NEMA 8 Stepper Lead Screw Linear Actuators (Non-Captive Type):
NEMA 8 Stepper Lead Screw Linear Actuators (Kaptive Type):
Stroke Specification of Kaptive Actuactor:
A(mm) | Stroke B (mm) | C(mm) | |
L=27.2 | L=38.1 | ||
11.2 | 9 | 1 | 0 |
14.9 | 12.7 | 5 | 0 |
21.1 | 19.05 | 11 | 0 |
27.6 | 25.4 | 17 | 6 |
34 | 31.8 | 24 | 13 |
40.3 | 38.1 | 30 | 19 |
Speed Thrust Curves:
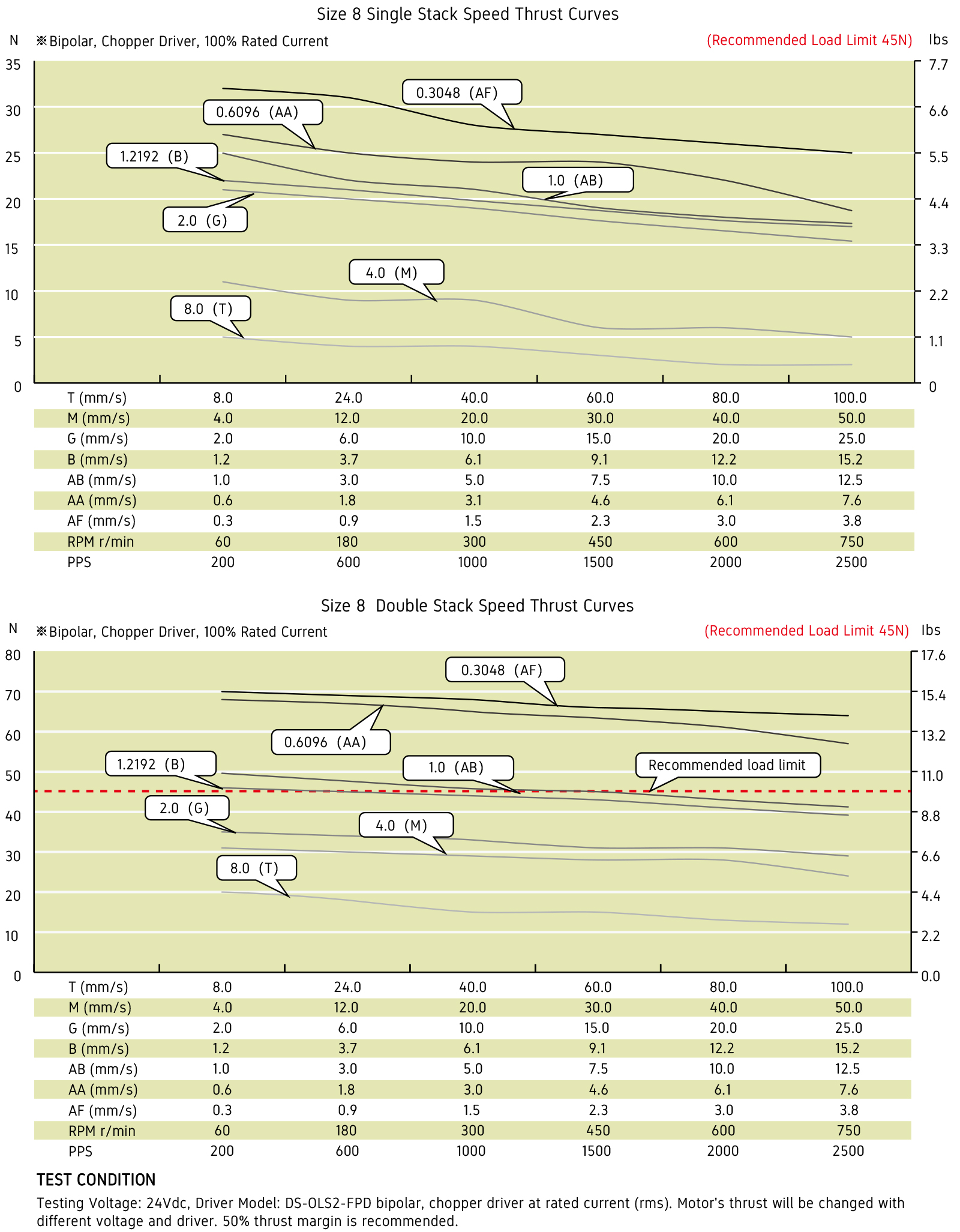
Options for screw end machining:
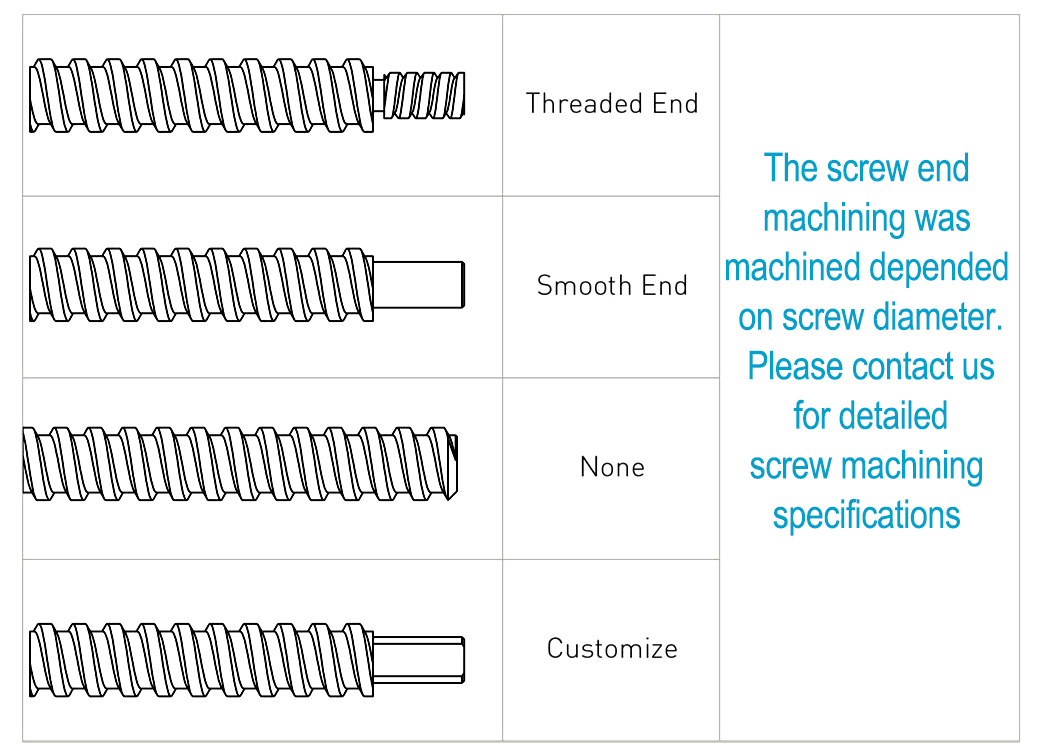
NEMA6 Stepper Lead Screw Linear Actuators
The NEMA 6 is our smallest hybrid linear actuators.
This compact unit can be integrated into various
Applications to provide precise linear positioning while
occupying less than 1 in2 of mouting footprint and
providing up to 44.5N of continuous thrust.
The Working Type for the Different Application Demand:
E: External Linear
N: Non-captive
C: Captive
K: Kaptive
Motor Characteristics:
Motor Code | Voltage (V) | Current (A) | Resistance (Ω) | Inductance (mH) | Weight (g) | Lead Wire No | Length (mm) |
6-30 | 6.6 | 0.3 | 22 | 3.6 | 50 | 4 | 30 |
6-28 | 2.45 | 0.5 | 4.9 | 1.5 | 48 | 4 | 28 |
6-38 | 5.5 | 0.5 | 11 | 2 | 55 | 4 | 38 |
Available Lead Screw and Travel per Step:
Lead Code | Screw Dia. (inch) | Screw Dia. (mm) | Lead (inch) | Lead (mm) | Travel Per Step @ 1.8 deg (mm) |
AF | 0.138 | 3.5 | 0.012 | 0.3048 | 0.0015 |
AA | 0.138 | 3.5 | 0.024 | 0.6096 | 0.003 |
B | 0.138 | 3.5 | 0.048 | 1.2192 | 0.0061 |
G | 0.138 | 3.5 | 0.079 | 2 | 0.01 |
M | 0.138 | 3.5 | 0.158 | 4 | 0.02 |
T | 0.138 | 3.5 | 0.315 | 8 | 0.04 |
NEMA 6 Stepper Lead Screw Linear Actuators (External Type):
NEMA6 Stepper Lead Screw Linear Actuators Speed Thrust Curves:
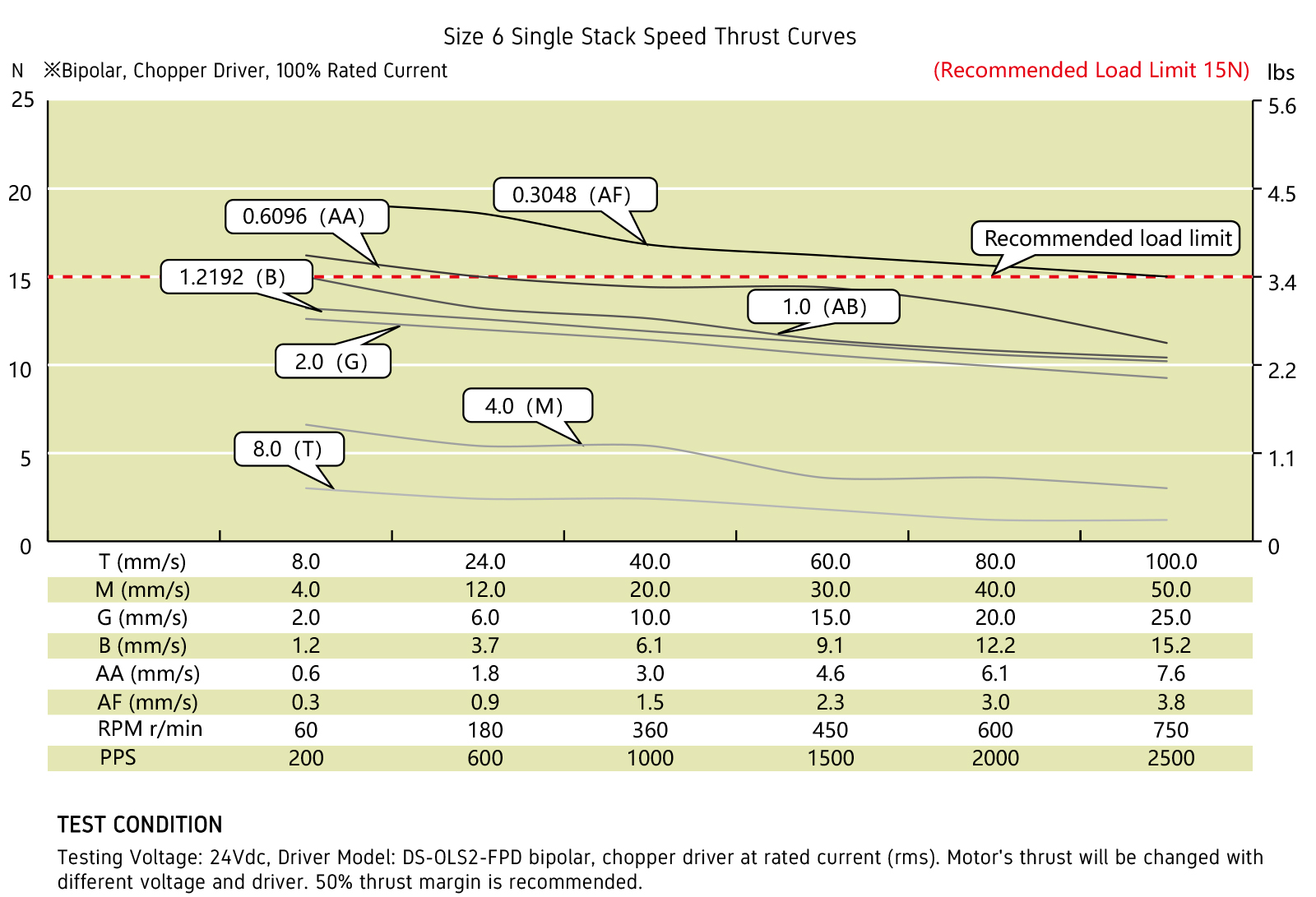
Options for screw end machining:
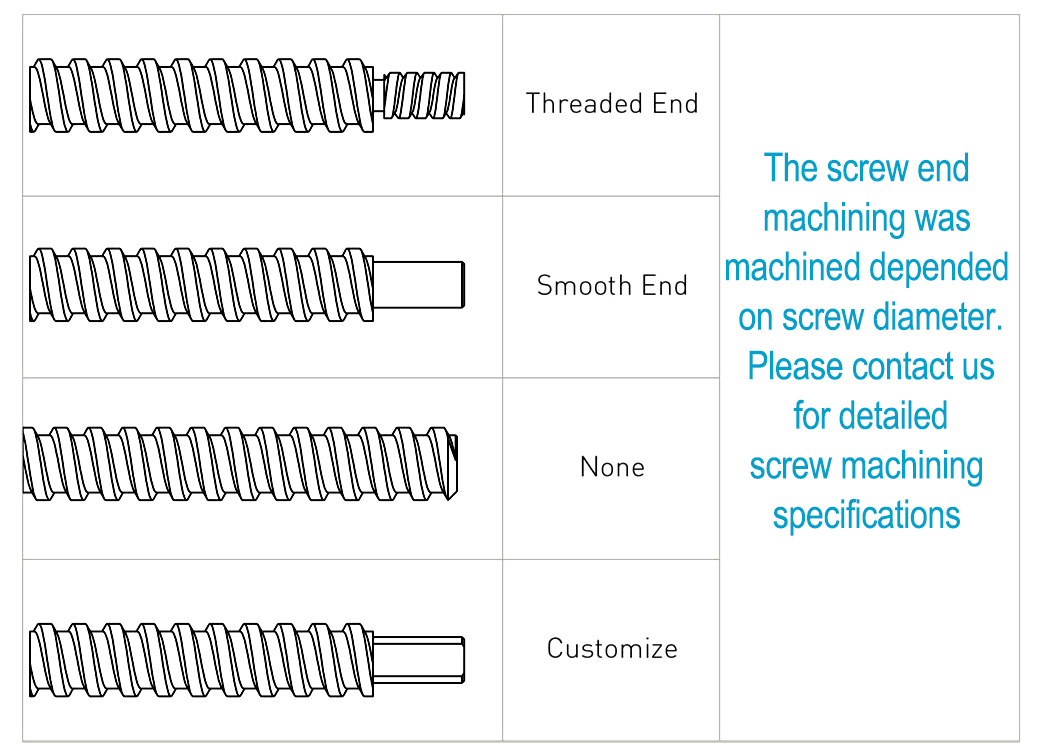
NEMA6 Stepper Ball Screw Linear Actuators
These actuators are external types have 6 different sizes, from 20mm to 57mm. From 0.005mm/
step to 0.1mm/step, variety of resolution for options available. Maximum thrust can reach 1600N.
Encoder option is available for whole Series
Motor size | NEMA8 | NEMA11 | NEMA14 | NEMA17 | NEMA23 | ||||
Dia. Lead | Φ4 | Φ5 | Φ6 | Φ6 | Φ8 | Φ6 | Φ8 | Φ10 | Φ12 |
1.0 mm | * | * | * | * | * | * | |||
2.0 mm | * | * | * | * | * | * | * | * | |
2.5 mm | * | * | |||||||
4.0 mm | * | * | |||||||
5.0 mm | * | * | * | ||||||
6.0 mm | * | * | * | ||||||
8.0 mm | * | * | |||||||
10.0 mm | * | * | * | * | * | * | * | ||
12.0 mm | * | * | |||||||
15.0 mm | * | ||||||||
20.0 mm | * |
NEMA6 Stepper Ball Screw Linear Actuators
Motor Characteristics:
Motor Code | Voltage (V) | Current (A) | Resistance (Ω) | Inductance (mH) | Weight (g) | Lead Wire No | Length (mm) |
6E2103 | 6.6 | 0.3 | 22 | 3.6 | 51 | 4 | 30 |
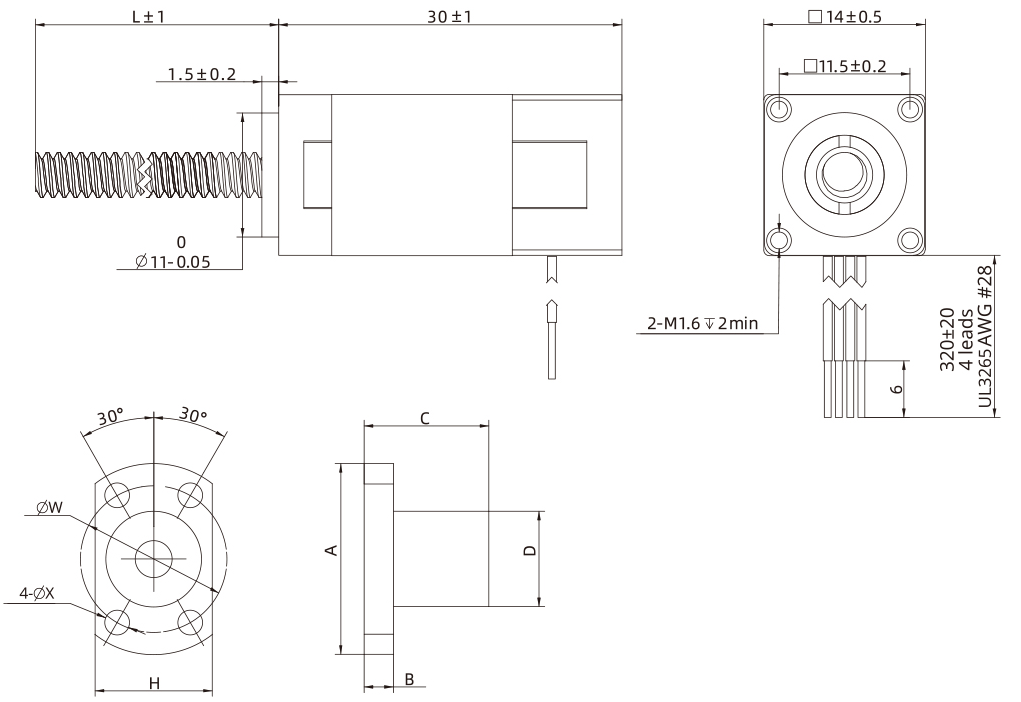
Ball screw type | SR0401 | SR0402 |
Ball Diameter | Ф0.8 | Ф0.8 |
Number of thread | 1 | |
Thread direction | Right | |
Shaft root dia. | Ф3.3 | |
Number of circuit | 3.7×1 | 2.7×1 |
Shat, nut material | SCM415H | |
Surface hardness | HRC58~62 | |
Anti-rust treatment | Anti-rust oil |
Nut size | A | B | C | D | H | W | X | Grade | Position accuracy | Total run out | Axial play | Dynamic load(N) | Static load(N) |
SR0401 | 23 | 4 | 17 | 11 | 15 | 17 | 3.4 | C7 | ±0.05 | 0.12 | 0.02 | 560 | 790 |
SR0402 | 23 | 4 | 19 | 11 | 15 | 17 | 3.4 | C7 | ±0.05 | 0.12 | 0.02 | 420 | 570 |
NEMA 6 Ball Screw Liner Stepper Motor Performance Curves:
Options for screw end machining:
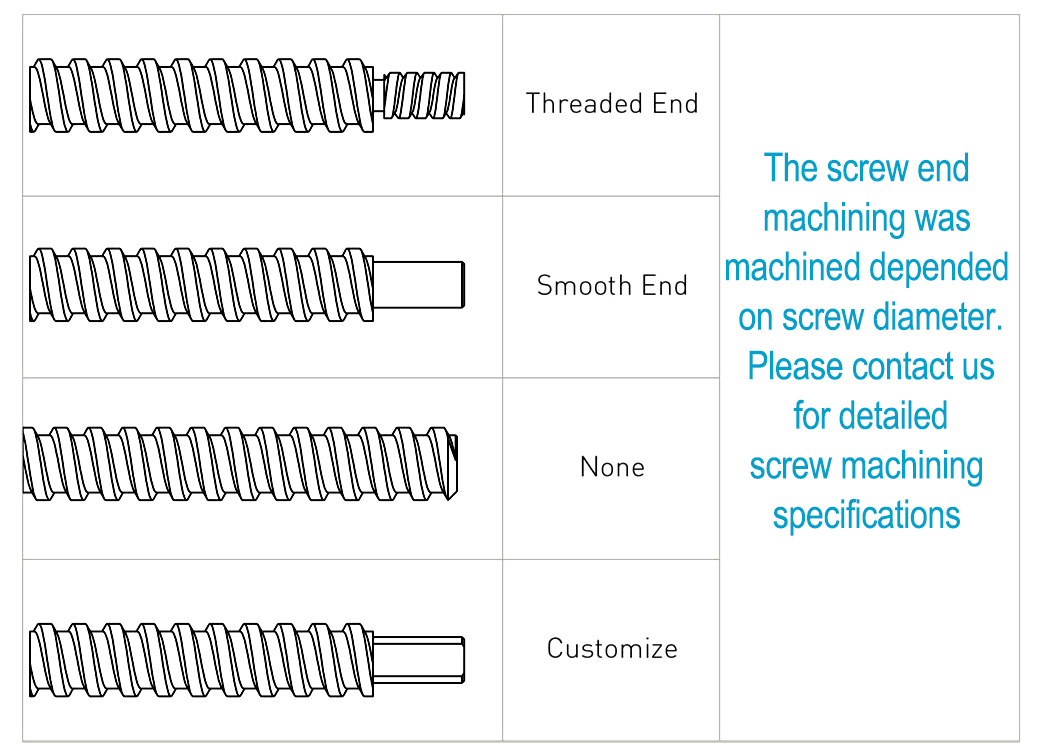
NEMA23 Stepper Ball Screw Linear Actuators
These actuators are external types have 5 different sizes, from 20mm to 57mm. From 0.005mm/
step to 0.1mm/step, variety of resolution for options available. Maximum thrust can reach 1600N.
Encoder option is available for whole Series
Motor size | NEMA8 | NEMA11 | NEMA14 | NEMA17 | NEMA23 | ||||
Dia. Lead | Φ4 | Φ5 | Φ6 | Φ6 | Φ8 | Φ6 | Φ8 | Φ10 | Φ12 |
1.0 mm | * | * | * | * | * | * | |||
2.0 mm | * | * | * | * | * | * | * | * | |
2.5 mm | * | * | |||||||
4.0 mm | * | * | |||||||
5.0 mm | * | * | * | ||||||
6.0 mm | * | * | * | ||||||
8.0 mm | * | * | |||||||
10.0 mm | * | * | * | * | * | * | * | ||
12.0 mm | * | * | |||||||
15.0 mm | * | ||||||||
20.0 mm | * |
NEMA23 Stepper Ball Screw Linear Actuators
Motor Characteristics:
Motor Code | Voltage (V) | Current (A) | Resistance (Ω) | Inductance (mH) | Lead Wire No | Length (mm) |
23E2110 | 6.4 | 1.0 | 6.4 | 16.4 | 4 | 45 |
23E2120 | 3.5 | 2.0 | 1.75 | 4.1 | 4 | 45 |
23E2130 | 2.4 | 3.0 | 0.8 | 1.7 | 4 | 45 |
23E2210 | 11.5 | 1.0 | 11.5 | 32 | 4 | 65 |
23E2225 | 5.0 | 2.5 | 2.0 | 5.2 | 4 | 65 |
23E2240 | 2.8 | 4.0 | 0.7 | 2.0 | 4 | 65 |
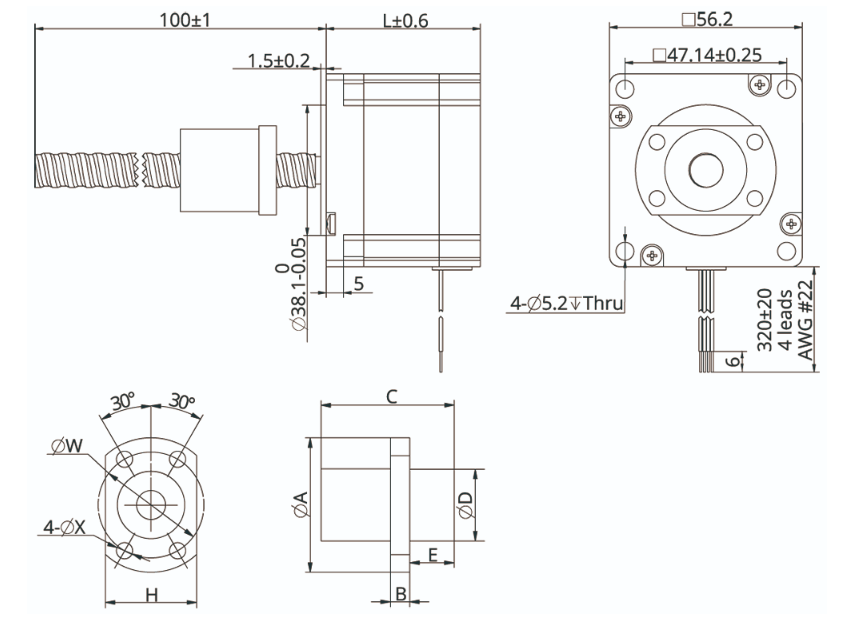
Ball screw type | 1002 | 1004 | 1005 | 1010 | 1015 | 1020 | 1202 | 1210 |
---|---|---|---|---|---|---|---|---|
Ball Size | Ф1.5875 | Ф2.0 | Ф2.0 | Ф2.0 | Ф2.0 | Ф1.5875 | Ф1.5875 | Ф2.381 |
Number of thread | 1 | 1 | 1 | 2 | 2 | 4 | 1 | 2 |
Thread direction | Right | |||||||
Shaft root dia. | Ф8.6 | Ф8.2 | Ф8.2 | Ф8.4 | Ф8.4 | Ф8.7 | Ф10.6 | Ф10.2 |
Number of circuit | 3.7×1 | 2.7×1 | 2.7×1 | 1.6×2 | 1.6×2 | 0.7×4 | 3.7×1 | 1.7 x 2 |
Shaft, nut material | SCM415H | |||||||
Surface hardness | HRC58~62 | |||||||
Anti-rust treatment | Anti-rust oil | |||||||
Grade | C7 |
Nut size | A | B | C | D | H | W | X | E | Position accuracy | Total run out | Axial play | Dynamic load[N] | Static load[N] |
---|---|---|---|---|---|---|---|---|---|---|---|---|---|
BS1002 | 40 | 5 | 24 | 23 | 25 | 32 | 4.5 | ±0.05 | 0.12 | ≤0.03 | 2700 | 5300 | |
BS1004 | 41 | 5 | 28 | 24 | 26 | 33 | 4.5 | ±0.05 | 0.12 | ≤0.03 | 3000 | 5200 | |
BS1005 | 40 | 5 | 26 | 23 | 25 | 32 | 4.5 | ±0.05 | 0.12 | ≤0.03 | 3000 | 5200 | |
BS1010 | 40 | 5 | 24 | 23 | 25 | 32 | 4.5 | 6 | ±0.05 | 0.12 | ≤0.03 | 3300 | 5900 |
BS1015 | 40 | 5 | 33 | 23 | 25 | 32 | 4.5 | 6 | ±0.05 | 0.12 | ≤0.03 | 3300 | 6400 |
BS1020 | 37 | 5 | 23 | 20 | 22 | 29 | 4.5 | 5 | ±0.05 | 0.12 | ≤0.03 | 2100 | 4000 |
BS1202 | 42 | 5 | 24 | 25 | 27 | 34 | 4.5 | ±0.05 | 0.12 | ≤0.03 | 3000 | 6400 | |
BS1210 | 41 | 5 | 30 | 24 | 26 | 33 | 4.5 | 9.5 | ±0.05 | 0.12 | ≤0.03 | 5100 | 9800 |
* The unit of Position accuracy, Total run out and Axial play is [mm].
NEMA 23 Ball Screw Liner Stepper Motor Performance Curves:
Options for screw end machining:
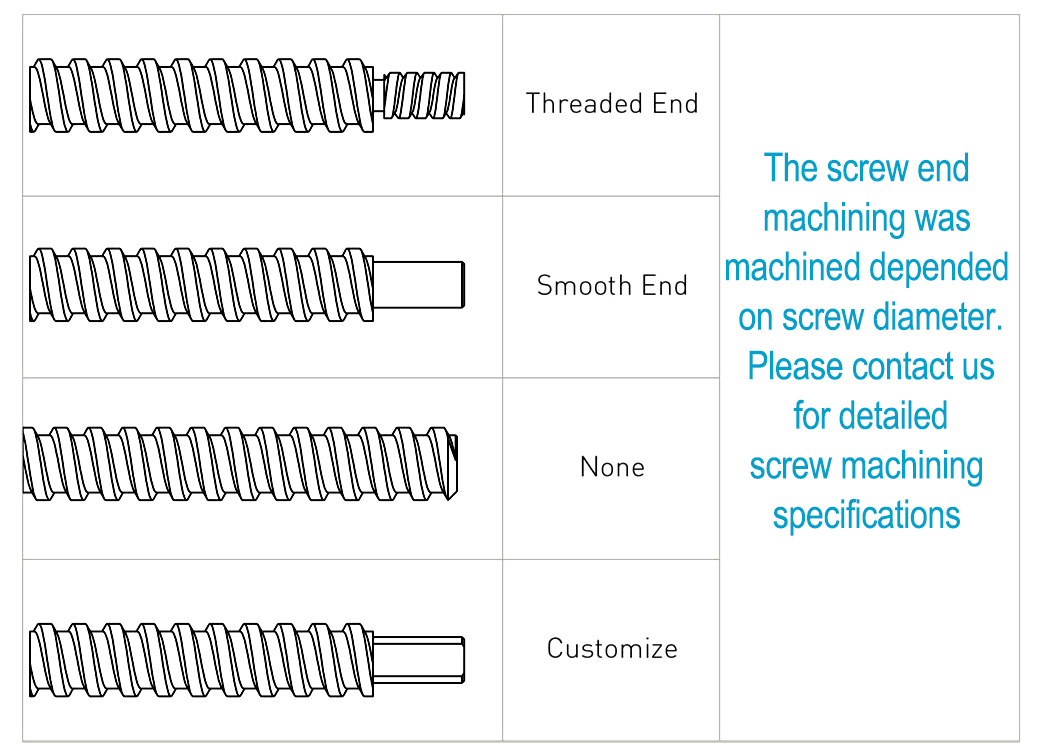
BLDC-6012S is a high-tech product used in the field of low-power motors with communication functions.
With the rapid development of electronic technology, the technology and performance of electronic products
are constantly updated and improved. The product uses super-large hardware integrated circuits, has high
anti-interference and fast response capabilities, and has the control performance of a traditional DC motor.
Compared with maintenance-free, long life and constant torque advantages.
Features
1. SPWM, Speed/Current alike close loop technology, smooth rotation
2. Smooth torque output within speed range (8000 rpm Max. )
3. 1:75 Max. speed regulation ratio
4. 60°/300°/120°/240°Electrical angle adjustable
5. Speed regulation: potentiometer adjust / Analog input
6. Run/Step、Quick Brake、CW/CCW rotation shift
7. Speed output、Alarm output(O. C. )
8. Over current、over voltage、stall、missing speed Alarm
Technical data
Electrical Parameters(Tj=25ºC) | |
Power | 24~60VDC, capacity: up to motors |
Current output | Rated 12A, Peak 36A(≤3s) |
Driving mode | SPWM |
Insulation Res | >500MΩ |
Dielectric Strength | 500V/min |
Weight | About 300g |
Environmental Requirements | |
Cooling method | Self cool |
Environment | Avoid dust, oil mist and corrosive gas |
Temperature | 0~ 50℃ |
Humidity | <80% RH, no condensation, no frosting |
Shock | 5.7m/s2 Max. |
Storage temp | -20~ 125°C |
Model Number:
Model No. | Power Supply Voltage | Continuous Output Current | Rated Power |
BLDC-6012S | 24VDC | 12A | 300W |
BLDC-6012A | 20VDC | 15A | 300W |
BLDC-50020 | 24VDC | 20A | 500W |
BLDC-50014 | 36VDC | 14A | 500W |
BLDC-50011 | 48VDC | 11A | 500W |
BLDC-4810 | 50VDC | 15A | 750W |
BLDC-10050 | 24VDC | 50A | 1500W |
BLDC-10033 | 36VDC | 33A | 1500W |
BLDC-10025 | 48VDC | 25A | 1500W |
BLDC-750H | 220VAC | 5A | 1000W |
↓Model Table:
MODEL TABLE | |
SW1=ON | HALL SENSOR |
SW1=OFF | None HALL SENSOR |
SW2=ON | 120°/240° Sensor Phasings |
SW2=OFF | 60°/300° Sensor Phasings |
SW3=ON | AVI port enable |
SW3=OFF | RV port enable |
VDC: 18V ~ 80V
External potentiometer speed governing:
AVI (Analog voltage or PWM frequency) speed governing:
RV speed governing:
Size:
NEMA8, NEMA11, NEMA14, NEMA17, NEMA23, NEMA23, NEMA34
20mm, 28mm, 35mm, 42mm, 57mm, 60mm, 86mm
Stepper
0.001524mm~0.16mm
Performance
Maximum thrust up to 240kg, low temperature rise, low vibration, low noise,
long life (up to 5 million cycles), and high positioning accuracy (up to ±0.005 mm)
Application
Medical diagnostic equipment, life science instruments, robots, optical equipment,
analytical instruments, semiconductor equipment, communication equipment, automation equipment
NEMA14 Lead Screw Linear Actuators
Linear Module, Linear Slider
Motor Type | Bipolar stepper |
Step Angle | 1.8° |
Voltage (V) | 1.4 / 2.9 |
Current (A) | 1.5 |
Resistance (Ohms) | 0.95 / 1.9 |
Inductance (mH) | 1.4 / 3.2 |
Lead Wires | 4 |
Motor Length (mm) | 34 / 47 |
Stroke (mm) | 30 / 60 / 90 |
Ambient Temperature | -20℃ ~ 50℃ |
Temperature Rise | 80K Max. |
Dielectric Strength | 1mA Max. @ 500V, 1KHz, 1Sec. |
Insulation Resistance | 100MΩ Min. @500Vdc |
Motor Characteristics:
Motor Size | Voltage/ Phase (V) | Current/ Phase (A) | Resistance/ Phase (Ω) | Inductance/ Phase (mH) | Number of Lead Wires | Rotor Inertia (g.cm2) | Motor Weight (g) | Motor Length L (mm) |
35 | 1.4 | 1.5 | 0.95 | 1.4 | 4 | 20 | 190 | 34 |
35 | 2.9 | 1.5 | 1.9 | 3.2 | 4 | 30 | 230 | 47 |
Available Lead Screw and Travel per Step:
Diameter (mm) | Lead (mm) | Step (mm) | Power off self-locking force (N) |
6.35 | 1.27 | 0.00635 | 150 |
6.35 | 3.175 | 0.015875 | 40 |
6.35 | 6.35 | 0.03175 | 15 |
6.35 | 12.7 | 0.0635 | 3 |
6.35 | 25.4 | 0.127 | 0 |
NEMA14 Linear Actuator outline drawing:
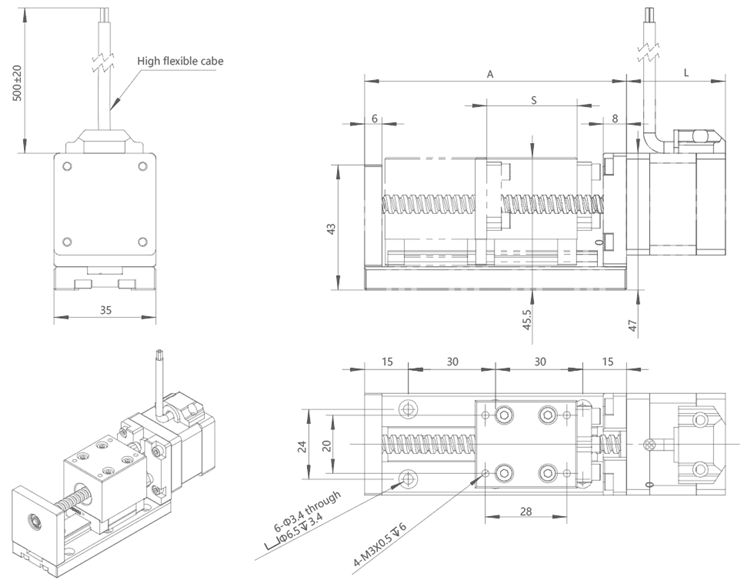
Stroke S (mm) | 30 | 60 | 90 |
Dimension A (mm) | 90 | 120 | 150 |
More Information on detail, please feel free to contact me 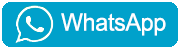
Size:
NEMA8, NEMA11, NEMA14, NEMA17, NEMA23, NEMA23, NEMA34
20mm, 28mm, 35mm, 42mm, 57mm, 60mm, 86mm
Stepper
0.001524mm~0.16mm
Performance
Maximum thrust up to 240kg, low temperature rise, low vibration, low noise,
long life (up to 5 million cycles), and high positioning accuracy (up to ±0.005 mm)
Application
Medical diagnostic equipment, life science instruments, robots, optical equipment,
analytical instruments, semiconductor equipment, communication equipment, automation equipment
NEMA11 Lead Screw Linear Actuators
Linear Module, Linear Slider
Motor Type | Bipolar stepper |
Step Angle | 1.8° |
Voltage (V) | 2.1 / 3.7 |
Current (A) | 1 |
Resistance (Ohms) | 2.1 / 3.7 |
Inductance (mH) | 1.5 / 2.3 |
Lead Wires | 4 |
Motor Length (mm) | 34 / 45 |
Stroke (mm) | 30 / 60 / 90 |
Ambient Temperature | -20℃ ~ 50℃ |
Temperature Rise | 80K Max. |
Dielectric Strength | 1mA Max. @ 500V, 1KHz, 1Sec. |
Insulation Resistance | 100MΩ Min. @500Vdc |
Motor Characteristics:
Motor Size | Voltage/ Phase (V) | Current/ Phase (A) | Resistance/ Phase (Ω) | Inductance/ Phase (mH) | Number of Lead Wires | Rotor Inertia (g.cm2) | Motor Weight (g) | Motor Length L (mm) |
28 | 2.1 | 1 | 2.1 | 1.5 | 4 | 9 | 120 | 34 |
28 | 3.7 | 1 | 3.7 | 2.3 | 4 | 13 | 180 | 45 |
Available Lead Screw and Travel per Step:
Diameter(mm) | Lead(mm) | Step(mm) | Power off self-locking force(N) |
4.76 | 0.635 | 0.003175 | 100 |
4.76 | 1.27 | 0.00635 | 40 |
4.76 | 2.54 | 0.0127 | 10 |
4.76 | 5.08 | 0.0254 | 1 |
4.76 | 10.16 | 0.0508 | 0 |
NEMA11 Linear Actuator outline drawing:
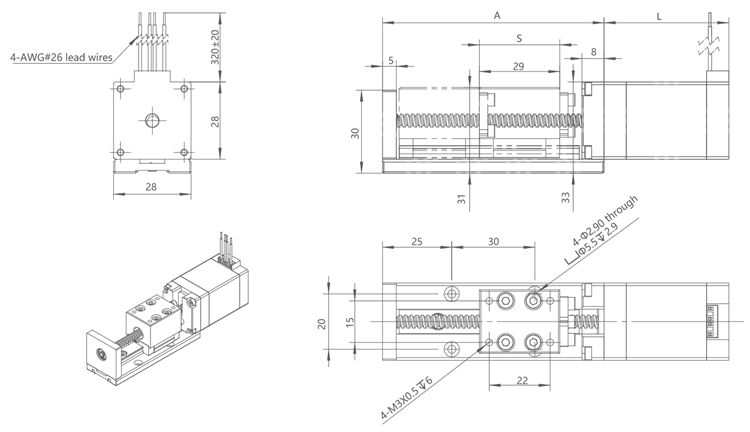
Stroke S (mm) | 30 | 60 | 90 |
Dimension A (mm) | 80 | 110 | 140 |
Size:
NEMA8, NEMA11, NEMA14, NEMA17, NEMA23, NEMA23, NEMA34
20mm, 28mm, 35mm, 42mm, 57mm, 60mm, 86mm
Stepper
0.001524mm~0.16mm
Performance
Maximum thrust up to 240kg, low temperature rise, low vibration, low noise,
long life (up to 5 million cycles), and high positioning accuracy (up to ±0.005 mm)
Application
Medical diagnostic equipment, life science instruments, robots, optical equipment,
analytical instruments, semiconductor equipment, communication equipment, automation equipment
NEMA17 Lead Screw Linear Actuators
Linear Module, Linear Slider
Motor Type | Bipolar stepper |
Step Angle | 1.8° |
Voltage (V) | 2.6 / 3.3 / 2 / 2.5 |
Current (A) | 1.5 / 1.5 / 2.5 / 2.5 |
Resistance (Ohms) | 1.8 / 2.2 / 0.8 / 1 |
Inductance (mH) | 2.6 / 4.6 / 1.8 / 2.8 |
Lead Wires | 4 |
Motor Length (mm) | 34 / 40 / 48 / 60 |
Stroke (mm) | 30 / 60 / 90 |
Ambient Temperature | -20℃ ~ 50℃ |
Temperature Rise | 80K Max. |
Dielectric Strength | 1mA Max. @ 500V, 1KHz, 1Sec. |
Insulation Resistance | 100MΩ Min. @500Vdc |
Motor Characteristics:
Motor Size | Voltage/ Phase (V) | Current/ Phase (A) | Resistance/ Phase (Ω) | Inductance/ Phase (mH) | Number of Lead Wires | Rotor Inertia (g.cm2) | Motor Weight (g) | Motor Length L (mm) |
42 | 2.6 | 1.5 | 1.8 | 2.6 | 4 | 35 | 250 | 34 |
42 | 3.3 | 1.5 | 2.2 | 4.6 | 4 | 55 | 290 | 40 |
42 | 2 | 2.5 | 0.8 | 1.8 | 4 | 70 | 385 | 48 |
42 | 2.5 | 2.5 | 1 | 2.8 | 4 | 105 | 450 | 60 |
Available Lead Screw and Travel per Step:
Diameter (mm) | Lead (mm) | Step (mm) | Power off self-locking force (N) |
6.35 | 1.27 | 0.00635 | 150 |
6.35 | 3.175 | 0.015875 | 40 |
6.35 | 6.35 | 0.03175 | 15 |
6.35 | 12.7 | 0.0635 | 3 |
6.35 | 25.4 | 0.127 | 0 |
NEMA17 Linear Actuator outline drawing:
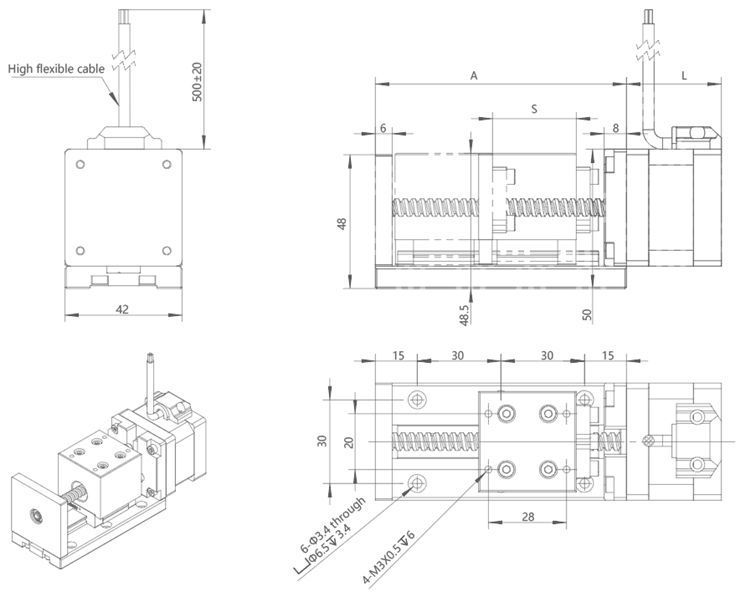
Stroke S (mm) | 30 | 60 | 90 |
Dimension A (mm) | 70 | 100 | 130 |
More Information on detail, please feel free to contact me 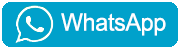
NEMA34 Stepper Lead Screw Linear Actuators
The NEMA 6 is our smallest hybrid linear actuators.
This compact unit can be integrated into various
Applications to provide precise linear positioning while
occupying less than 1 in2 of mounting footprint and
providing up to 44.5N of continuous thrust.
The Working Type for the Different Application Demand:
E: External Linear
N: Non-captive
C: Captive
K: Kaptive
Motor Characteristics:
Motor | Voltage[V] | Current[A] | Resistance[Ω] | Inductance[mH] | Weight[g] | Lead Wire No. | Motor Length[mm] |
---|---|---|---|---|---|---|---|
34-2113 | 12 | 1.3 | 9.2 | 71 | 2370 | 4 | 76 |
34-2130 | 5.7 | 3 | 1.9 | 15 | 2370 | 4 | 76 |
34-2155 | 2.85 | 5.5 | 0.52 | 4.5 | 2370 | 4 | 76 |
Available Lead Screw and Travel per Step:
Screw Dia.[inch] | Screw Dia.[mm] | Lead[inch] | Lead[mm] | Lead Code | Travel Per Step @ 1.8° [mm]* | Travel Per Step @ 0.9° [mm]* |
---|---|---|---|---|---|---|
0.625 | 15.875 | 0.1 | 2.54 | K | 0.0127 | 0.0064 |
0.625 | 15.875 | 0.125 | 3.175 | L | 0.0159 | 0.0079 |
0.625 | 15.875 | 0.2 | 5.08 | R | 0.0254 | 0.0127 |
0.625 | 15.875 | 0.25 | 6.35 | S | 0.0318 | 0.0159 |
0.625 | 15.875 | 0.5 | 12.7 | Y | 0.0635 | 0.0318 |
0.625 | 15.875 | 1 | 25.4 | Z | 0.127 | 0.0635 |
NEMA 34 Stepper Lead Screw Linear Actuators (External Type):
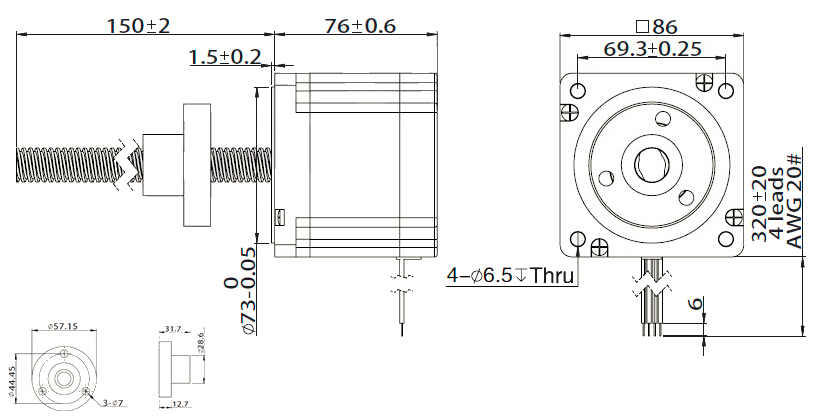
NEMA 34 Stepper Lead Screw Linear Actuators (Non-Captive Type):
Speed Thrust Curves:
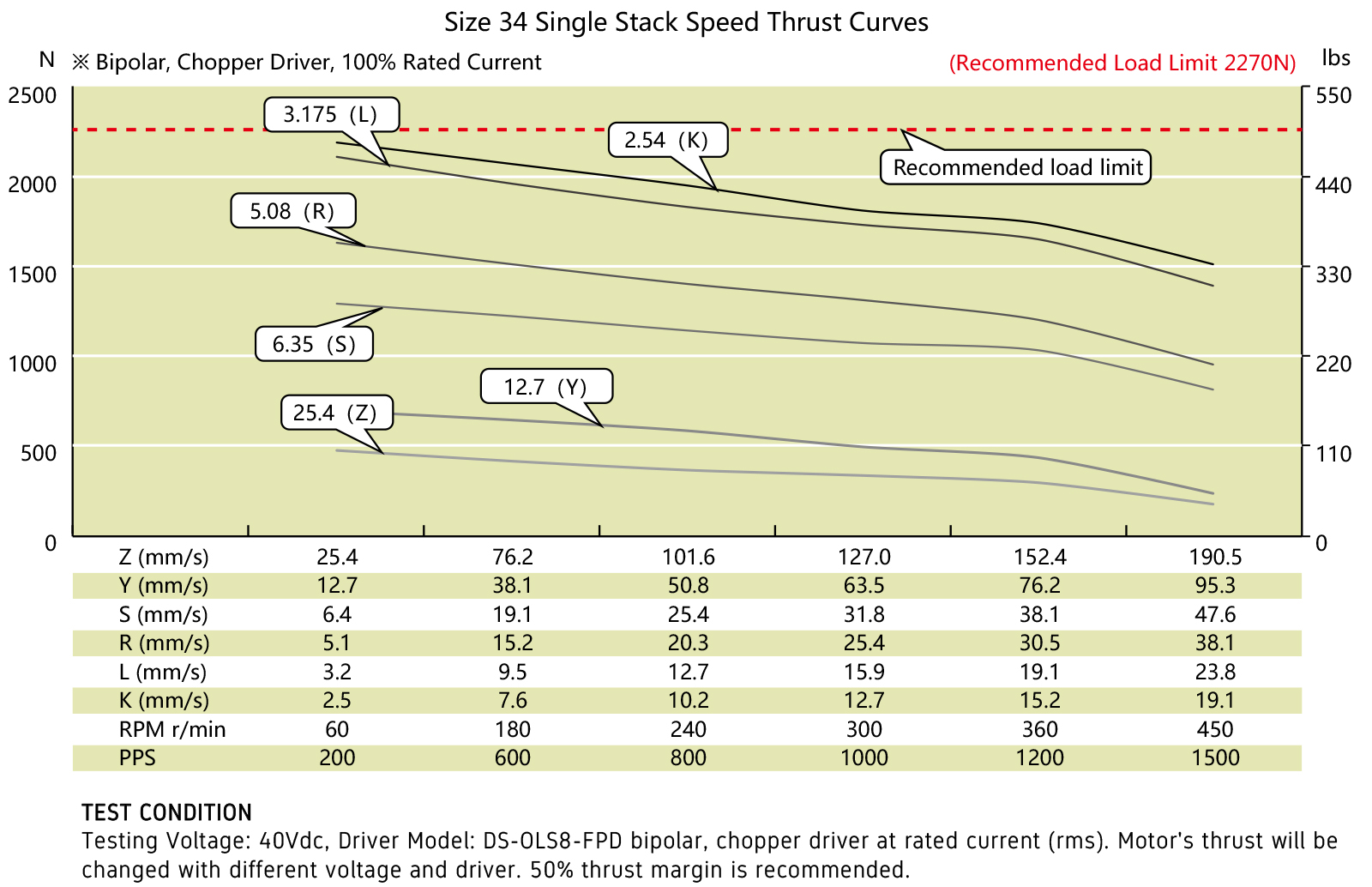
Options for screw end machining:
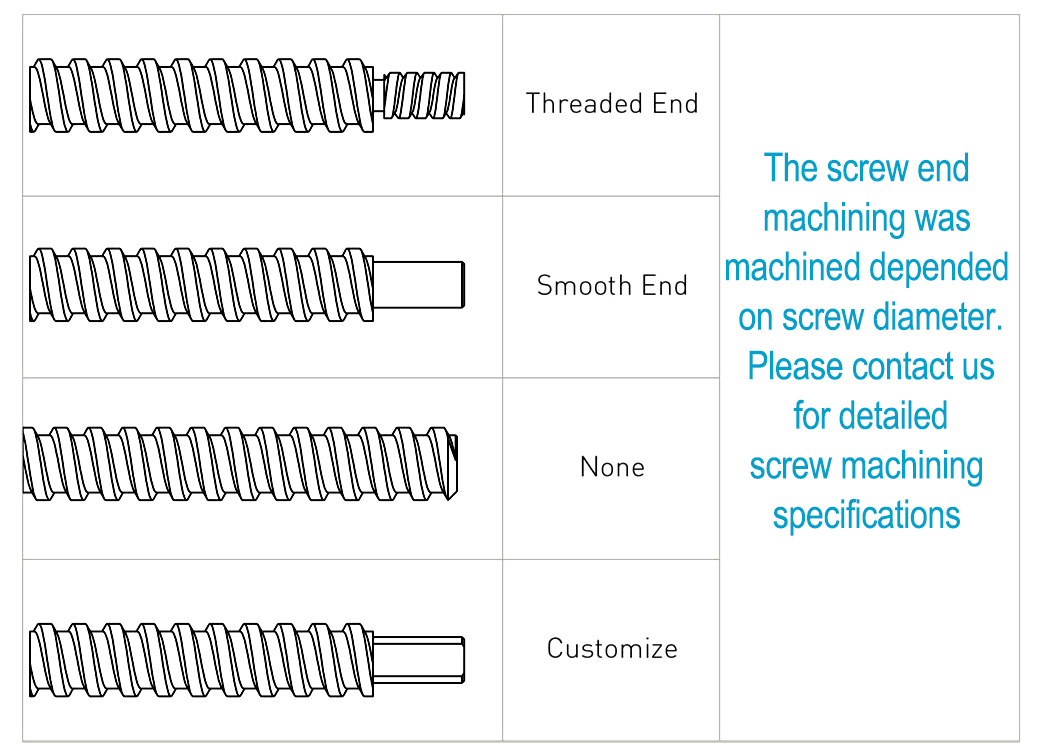
NEMA24 Stepper Lead Screw Linear Actuators
The NEMA 6 is our smallest hybrid linear actuators.
This compact unit can be integrated into various
Applications to provide precise linear positioning while
occupying less than 1 in2 of mounting footprint and
providing up to 44.5N of continuous thrust.
The Working Type for the Different Application Demand:
E: External Linear
N: Non-captive
C: Captive
K: Kaptive
Motor Characteristics:
Motor | Voltage[V] | Current[A] | Resistance[Ω] | Inductance[mH] | Weight[g] | Lead Wire No. | Motor Length[mm] |
---|---|---|---|---|---|---|---|
24-2120 | 3 | 2 | 1.5 | 3.9 | 680 | 4 | 47 |
24-2130 | 1.8 | 3 | 0.6 | 1.6 | 680 | 4 | 47 |
24-2140 | 1.6 | 4 | 0.4 | 0.9 | 680 | 4 | 47 |
24-2230 | 3 | 3 | 1 | 3.4 | 1080 | 4 | 68.3 |
24-2240 | 2.4 | 4 | 0.6 | 1.9 | 1080 | 4 | 68.3 |
24-2250 | 1.5 | 5 | 0.3 | 1.2 | 1080 | 4 | 68.3 |
Available Lead Screw and Travel per Step:
Screw Dia.[inch] | Screw Dia.[mm] | Lead[inch] | Lead[mm] | Lead Code | Travel Per Step @ 1.8° [mm]* | Travel Per Step @ 0.9° [mm]* |
---|---|---|---|---|---|---|
0.394 | 10 | 0.079 | 2 | G | 0.01 | 0.005 |
0.375 | 9.525 | 0.025 | 0.635 | A | 0.0032 | 0.0016 |
0.375 | 9.525 | 0.05 | 1.27 | D | 0.0064 | 0.0032 |
0.375 | 9.525 | 0.0625 | 1.5875 | F | 0.0079 | 0.004 |
0.375 | 9.525 | 0.083 | 2.1167 | H | 0.0106 | 0.0053 |
0.375 | 9.525 | 0.1 | 2.54 | K | 0.0127 | 0.0064 |
0.375 | 9.525 | 0.125 | 3.175 | L | 0.0159 | 0.0079 |
0.375 | 9.525 | 0.167 | 4.2333 | P | 0.0212 | 0.0106 |
0.375 | 9.525 | 0.2 | 5.08 | R | 0.0254 | 0.0127 |
0.375 | 9.525 | 0.25 | 6.35 | S | 0.0318 | 0.0159 |
0.375 | 9.525 | 0.375 | 9.525 | V | 0.0476 | 0.0238 |
0.375 | 9.525 | 0.384 | 9.7536 | W | 0.0488 | 0.0244 |
0.375 | 9.525 | 0.4 | 10.16 | X | 0.0508 | 0.0254 |
0.375 | 9.525 | 0.5 | 12.7 | Y | 0.0635 | 0.0318 |
0.375 | 9.525 | 1 | 25.4 | Z | 0.127 | 0.0635 |
NEMA 24 Stepper Lead Screw Linear Actuators (External Type):
NEMA 24 Stepper Lead Screw Linear Actuators (Non-Captive Type):
NEMA 24 Stepper Lead Screw Linear Actuators (Captive Type):
Stroke Specification of Captive Actuactor:
A(mm) | Stroke B (mm) | L(mm) | |
SingleStack | DoubleStack | ||
45.70 | 12.70 | 45 | 65 |
52.05 | 19.05 | 45 | 65 |
58.40 | 25.40 | 45 | 65 |
64.80 | 31.80 | 45 | 65 |
71.10 | 38.10 | 45 | 65 |
83.80 | 50.80 | 45 | 65 |
96.50 | 63.50 | 45 | 65 |
NEMA 24 Stepper Lead Screw Linear Actuators (Kaptive Type):
Stroke Specification of Kaptive Actuactor:
Size A (mm) | Stroke B (mm) | C (mm) | |
---|---|---|---|
Single Stack L=45 | Double Stack L=65 | ||
24.20 | 12.70 | 5.80 | 0.00 |
30.55 | 19.05 | 12.15 | 2.15 |
36.90 | 25.40 | 18.50 | 8.50 |
43.25 | 31.75 | 24.85 | 14.85 |
49.60 | 38.10 | 31.20 | 21.20 |
62.30 | 50.80 | 43.90 | 33.90 |
75.00 | 63.50 | 56.60 | 46.60 |
Speed Thrust Curves:
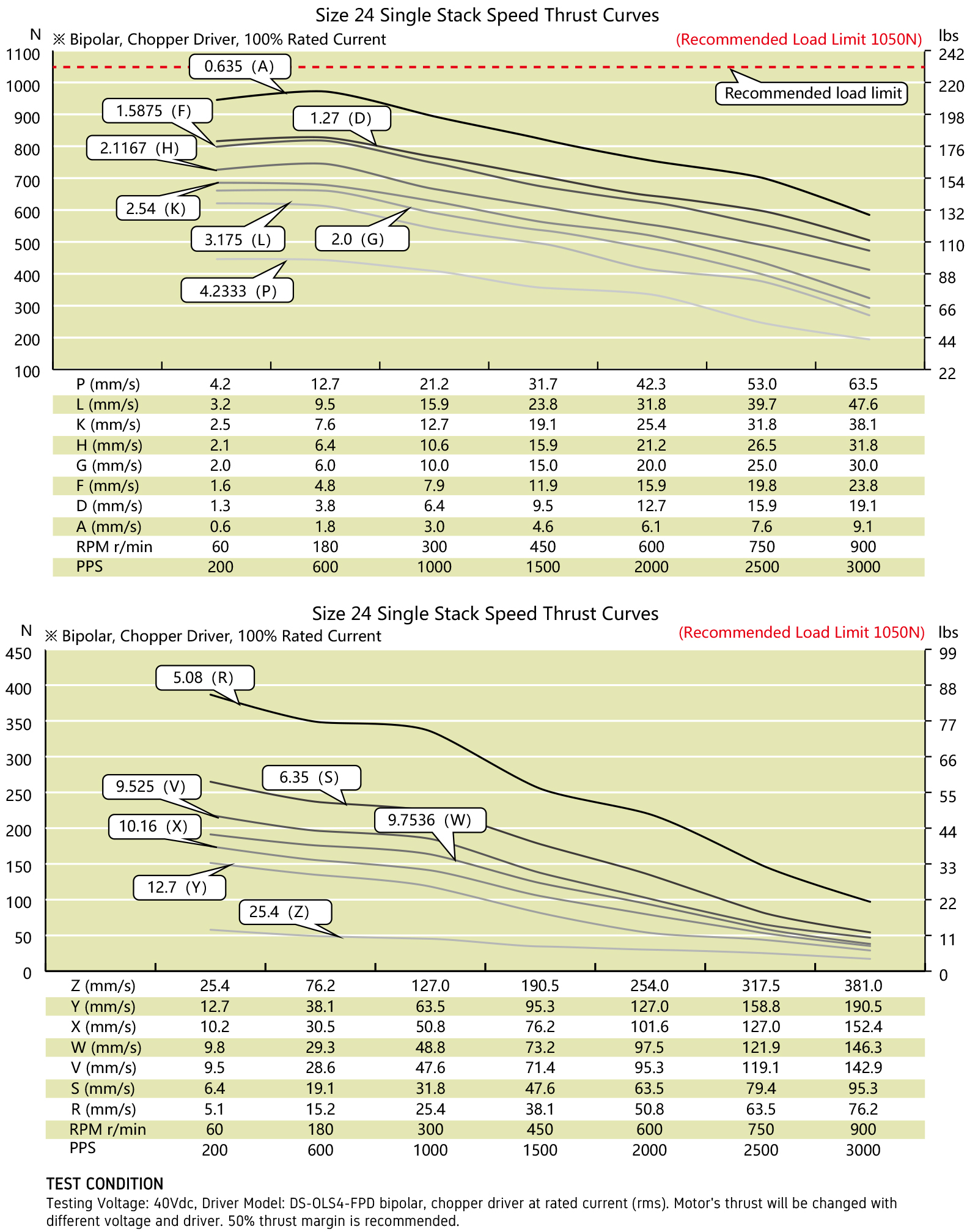
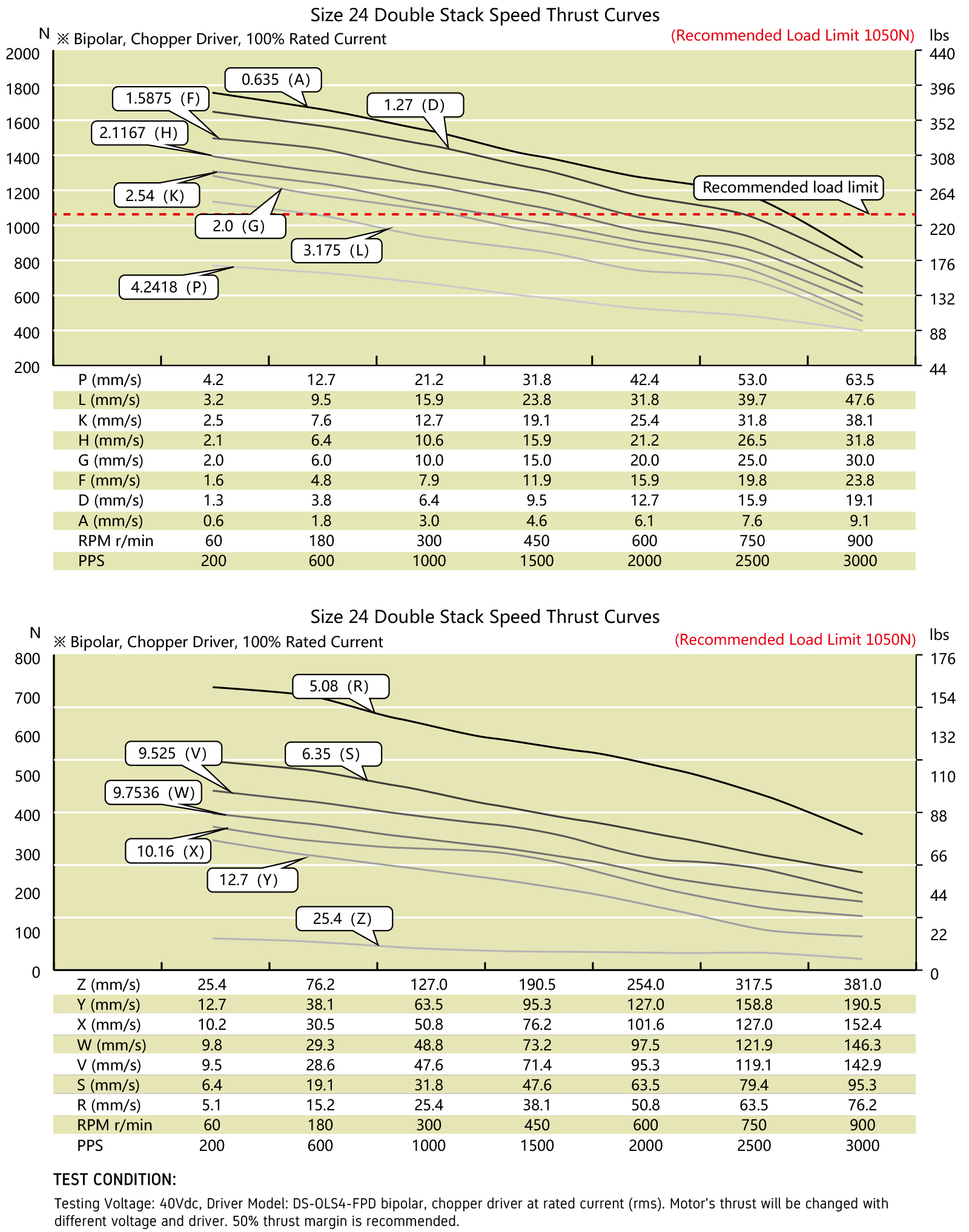
Options for screw end machining:
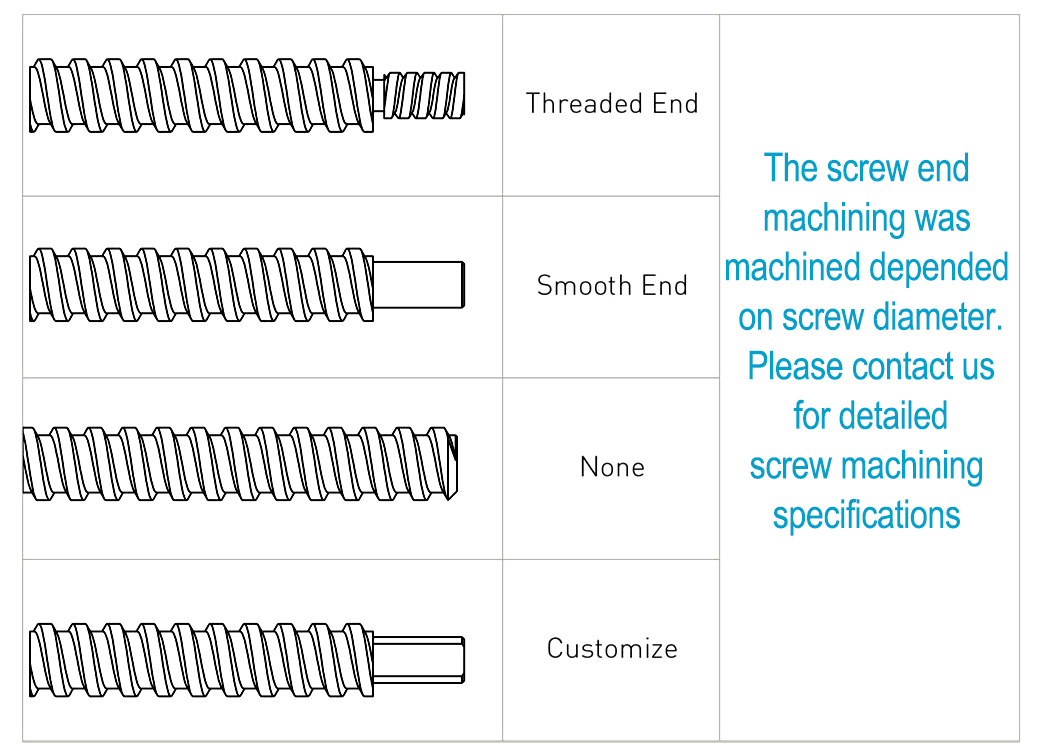
NEMA23 Stepper Lead Screw Linear Actuators
The NEMA 6 is our smallest hybrid linear actuators.
This compact unit can be integrated into various
Applications to provide precise linear positioning while
occupying less than 1 in2 of mounting footprint and
providing up to 44.5N of continuous thrust.
The Working Type for the Different Application Demand:
E: External Linear
N: Non-captive
C: Captive
K: Kaptive
Motor Characteristics:
Motor | Voltage[V] | Current[A] | Resistance[Ω] | Inductance[mH] | Weight[g] | Lead Wire No. | Motor Length[mm] |
---|---|---|---|---|---|---|---|
23-2110 | 6.4 | 1 | 6.4 | 16.4 | 585 | 4 | 45 |
23-2120 | 3.5 | 2 | 1.75 | 4.1 | 585 | 4 | 45 |
23-2130 | 2.4 | 3 | 0.8 | 1.7 | 585 | 4 | 45 |
23-2210 | 11.5 | 1 | 11.5 | 32 | 880 | 4 | 65 |
23-2225 | 5 | 2.5 | 2 | 5.2 | 880 | 4 | 65 |
23-2240 | 2.8 | 4 | 0.7 | 2 | 880 | 4 | 65 |
Available Lead Screw and Travel per Step:
Screw Dia.[inch] | Screw Dia.[mm] | Lead[inch] | Lead[mm] | Lead Code | Travel Per Step @ 1.8° [mm]* | Travel Per Step @ 0.9° [mm]* |
---|---|---|---|---|---|---|
0.394 | 10 | 0.079 | 2 | G | 0.01 | 0.005 |
0.375 | 9.525 | 0.025 | 0.635 | A | 0.0032 | 0.0016 |
0.375 | 9.525 | 0.05 | 1.27 | D | 0.0064 | 0.0032 |
0.375 | 9.525 | 0.0625 | 1.5875 | F | 0.0079 | 0.004 |
0.375 | 9.525 | 0.083 | 2.1167 | H | 0.0106 | 0.0053 |
0.375 | 9.525 | 0.1 | 2.54 | K | 0.0127 | 0.0064 |
0.375 | 9.525 | 0.125 | 3.175 | L | 0.0159 | 0.0079 |
0.375 | 9.525 | 0.167 | 4.2333 | P | 0.0212 | 0.0106 |
0.375 | 9.525 | 0.2 | 5.08 | R | 0.0254 | 0.0127 |
0.375 | 9.525 | 0.25 | 6.35 | S | 0.0318 | 0.0159 |
0.375 | 9.525 | 0.375 | 9.525 | V | 0.0476 | 0.0238 |
0.375 | 9.525 | 0.384 | 9.7536 | W | 0.0488 | 0.0244 |
0.375 | 9.525 | 0.4 | 10.16 | X | 0.0508 | 0.0254 |
0.375 | 9.525 | 0.5 | 12.7 | Y | 0.0635 | 0.0318 |
0.375 | 9.525 | 1 | 25.4 | Z | 0.127 | 0.0635 |
NEMA 23 Stepper Lead Screw Linear Actuators (External Type):
NEMA 23 Stepper Lead Screw Linear Actuators (Non-Captive Type):
NEMA 23 Stepper Lead Screw Linear Actuators (Captive Type):
Stroke Specification of Captive Actuactor:
A(mm) | Stroke B (mm) | L(mm) | |
SingleStack | DoubleStack | ||
45.70 | 12.70 | 45 | 65 |
52.05 | 19.05 | 45 | 65 |
58.40 | 25.40 | 45 | 65 |
64.80 | 31.80 | 45 | 65 |
71.10 | 38.10 | 45 | 65 |
83.80 | 50.80 | 45 | 65 |
96.50 | 63.50 | 45 | 65 |
NEMA 23 Stepper Lead Screw Linear Actuators (Kaptive Type):
Stroke Specification of Kaptive Actuactor:
Size A (mm) | Stroke B (mm) | C (mm) | |
---|---|---|---|
Single Stack L=45 | Double Stack L=65 | ||
24.20 | 12.70 | 5.80 | 0.00 |
30.55 | 19.05 | 12.15 | 2.15 |
36.90 | 25.40 | 18.50 | 8.50 |
43.25 | 31.75 | 24.85 | 14.85 |
49.60 | 38.10 | 31.20 | 21.20 |
62.30 | 50.80 | 43.90 | 33.90 |
75.00 | 63.50 | 56.60 | 46.60 |
Speed Thrust Curves:
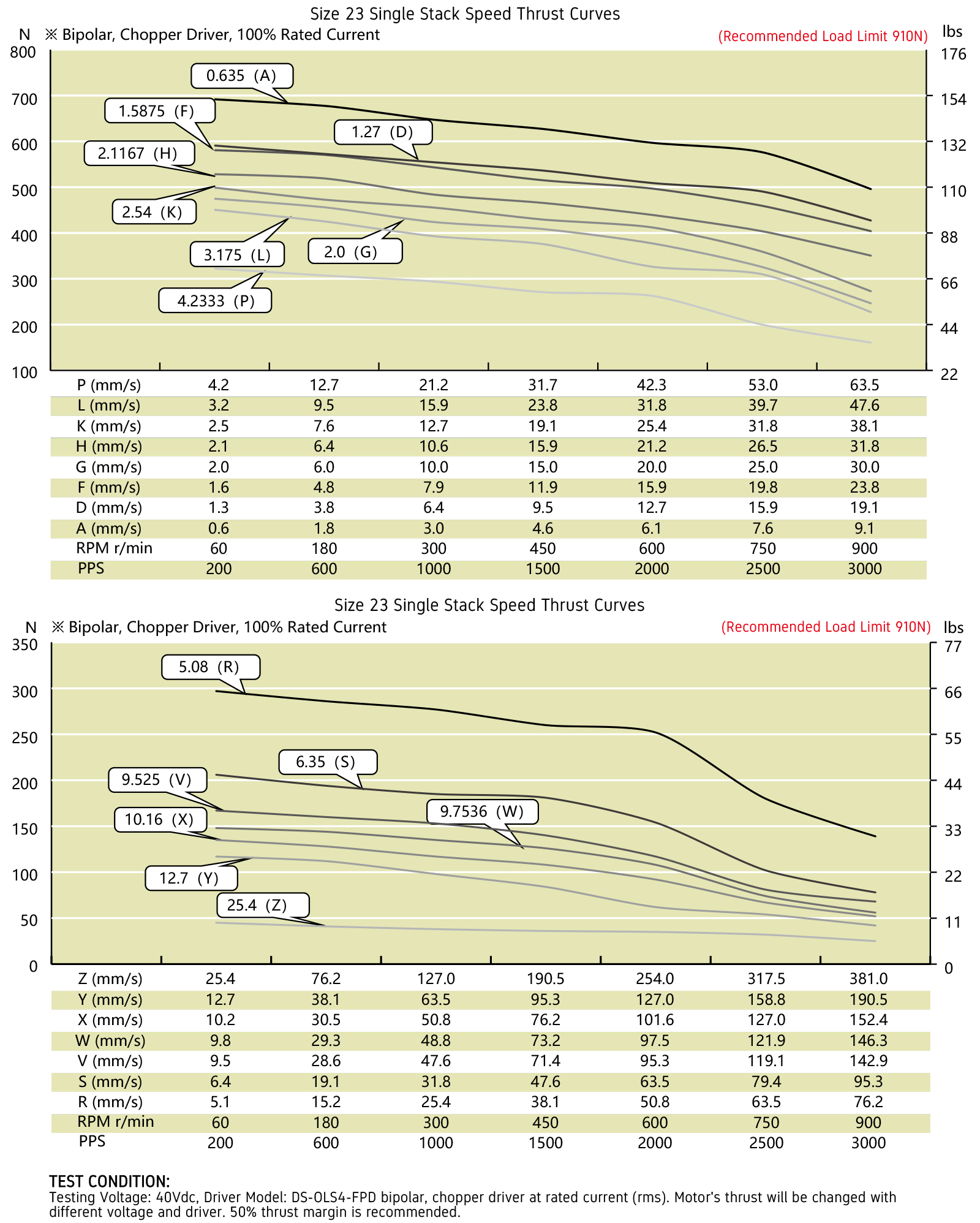
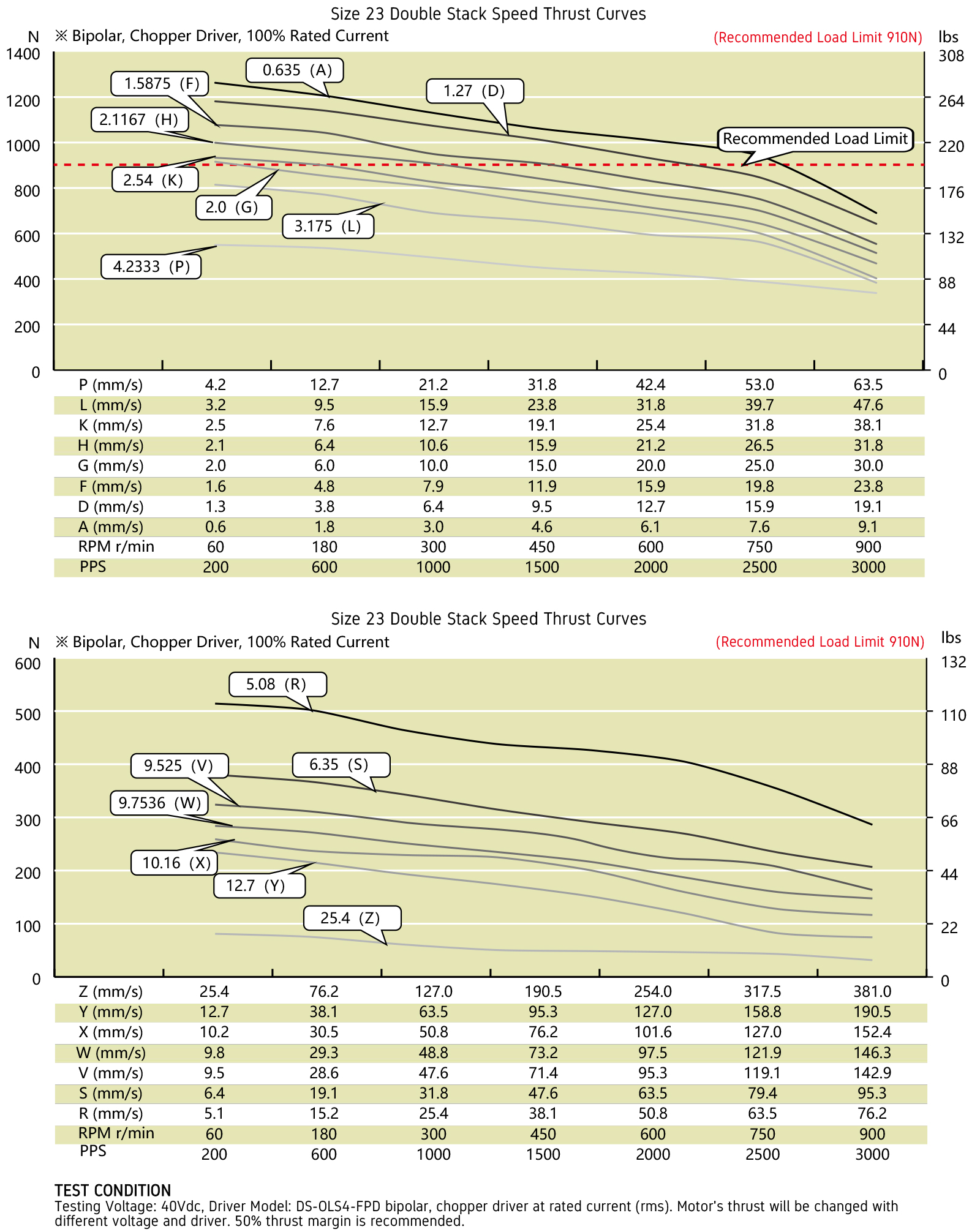
Options for screw end machining:
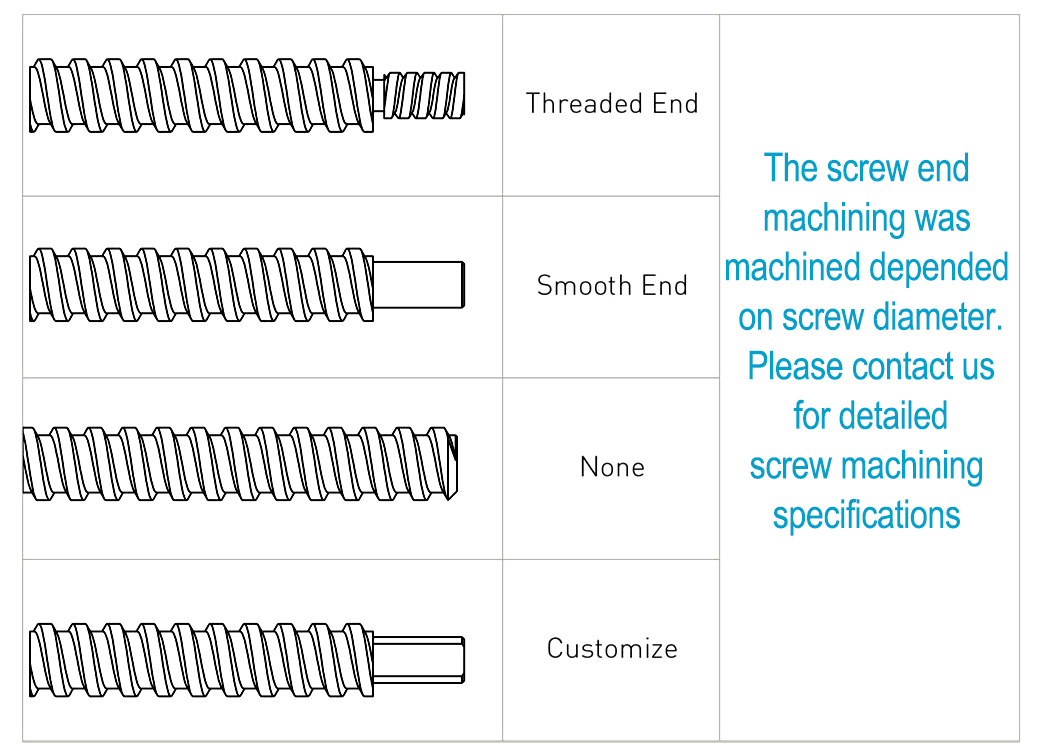
NEMA17 Stepper Lead Screw Linear Actuators
The NEMA 6 is our smallest hybrid linear actuators.
This compact unit can be integrated into various
Applications to provide precise linear positioning while
occupying less than 1 in2 of mounting footprint and
providing up to 44.5N of continuous thrust.
The Working Type for the Different Application Demand:
E: External Linear
N: Non-captive
C: Captive
K: Kaptive
Motor Characteristics:
Motor Code | Voltage (V) | Current (A) | Resistance (Ω) | Inductance (mH) | Weight (g) | Lead Wire No | Length (mm) |
17-2105 | 7.2 | 0.5 | 14.4 | 19.8 | 254 | 4 | 34.1 |
17-2110 | 3.6 | 1 | 3.6 | 5 | 254 | 4 | 34.1 |
17-2115 | 2.4 | 1.5 | 1.9 | 2.2 | 254 | 4 | 34.1 |
17-2205 | 11 | 0.5 | 22 | 46 | 386 | 4 | 48.1 |
17-2212 | 4.5 | 1.2 | 3.8 | 8 | 386 | 4 | 48.1 |
17-2225 | 2.2 | 2.5 | 0.9 | 1.8 | 386 | 4 | 48.1 |
Available Lead Screw and Travel per Step:
Screw Dia.[inch] | Screw Dia.[mm] | Lead[inch] | Lead[mm] | Lead Code | Travel Per Step @ 1.8° [mm]* | Travel Per Step @ 0.9° [mm]* |
---|---|---|---|---|---|---|
0.25 | 6.35 | 0.024 | 0.6096 | AA | 0.003 | 0.0015 |
0.25 | 6.35 | 0.0394 | 1 | AB | 0.005 | 0.0025 |
0.25 | 6.35 | 0.048 | 1.2192 | B | 0.006 | 0.003 |
0.25 | 6.35 | 0.05 | 1.27 | D | 0.0064 | 0.0032 |
0.25 | 6.35 | 0.0625 | 1.5875 | F | 0.0079 | 0.004 |
0.25 | 6.35 | 0.096 | 2.4384 | J | 0.0122 | 0.0061 |
0.25 | 6.35 | 0.1 | 2.54 | K* | 0.0127 | 0.0064 |
0.25 | 6.35 | 0.125 | 3.175 | L* | 0.0159 | 0.0079 |
0.25 | 6.35 | 0.192 | 4.8768 | Q | 0.024 | 0.0122 |
0.375 | 6.35 | 0.2 | 5.08 | R* | 0.0254 | 0.0127 |
0.25 | 6.35 | 0.25 | 6.35 | S* | 0.0318 | 0.0159 |
0.25 | 6.35 | 0.3333 | 8.4667 | U | 0.0423 | 0.0212 |
0.25 | 6.35 | 0.384 | 9.7536 | W* | 0.0488 | 0.0244 |
0.25 | 6.35 | 0.5 | 12.7 | Y* | 0.0635 | 0.0318 |
0.25 | 6.35 | 1.0 | 25.4 | Z* | 0.127 | 0.0635 |
0.31 | 8 | 0.1575 | 4 | M | 0.02 | 0.01 |
0.31 | 8 | 0.315 | 8 | T | 0.04 | 0.02 |
0.31 | 8 | 0.0787 | 2 | G | 0.01 | 0.005 |
NEMA 17 Stepper Lead Screw Linear Actuators (External Type):
NEMA 17 Stepper Lead Screw Linear Actuators (Non-Captive Type):
NEMA 17 Stepper Lead Screw Linear Actuators (Captive Type):
Stroke Specification of Captive Actuactor:
Size A (mm) | Stroke B (mm) | L (mm) | |
---|---|---|---|
35.70 | 12.70 | Single Stack Motor 34.1 | Double Stack Motor 48.1 |
42.05 | 19.05 | ||
48.40 | 25.40 | ||
54.80 | 31.80 | ||
61.10 | 38.10 | ||
73.80 | 50.80 | ||
86.50 | 63.5 |
NEMA 17 Stepper Lead Screw Linear Actuators (Kaptive Type):
Stroke Specification of Kaptive Actuactor:
Size A (mm) | Stroke B (mm) | C (mm) | |
---|---|---|---|
Single Stack L=34.1 | Double Stack L=48.1 | ||
18.50 | 12.70 | 4.10 | 0.00 |
24.85 | 19.05 | 10.45 | 5.45 |
31.20 | 25.40 | 16.80 | 11.80 |
37.55 | 31.75 | 23.15 | 18.15 |
43.90 | 38.10 | 29.50 | 24.5 |
56.60 | 50.80 | 42.20 | 37.20 |
69.30 | 63.50 | 54.90 | 49.90 |
Speed Thrust Curves:
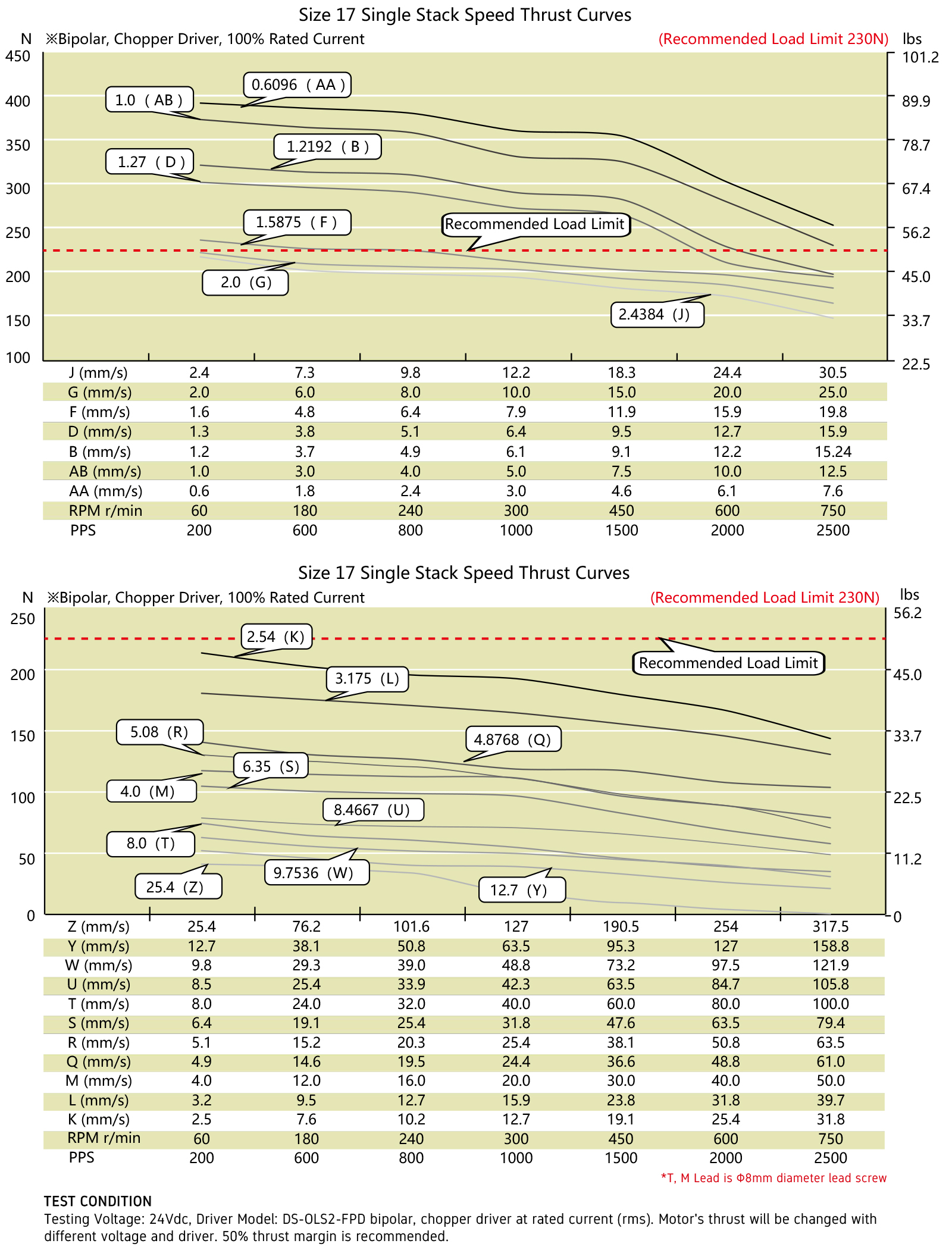
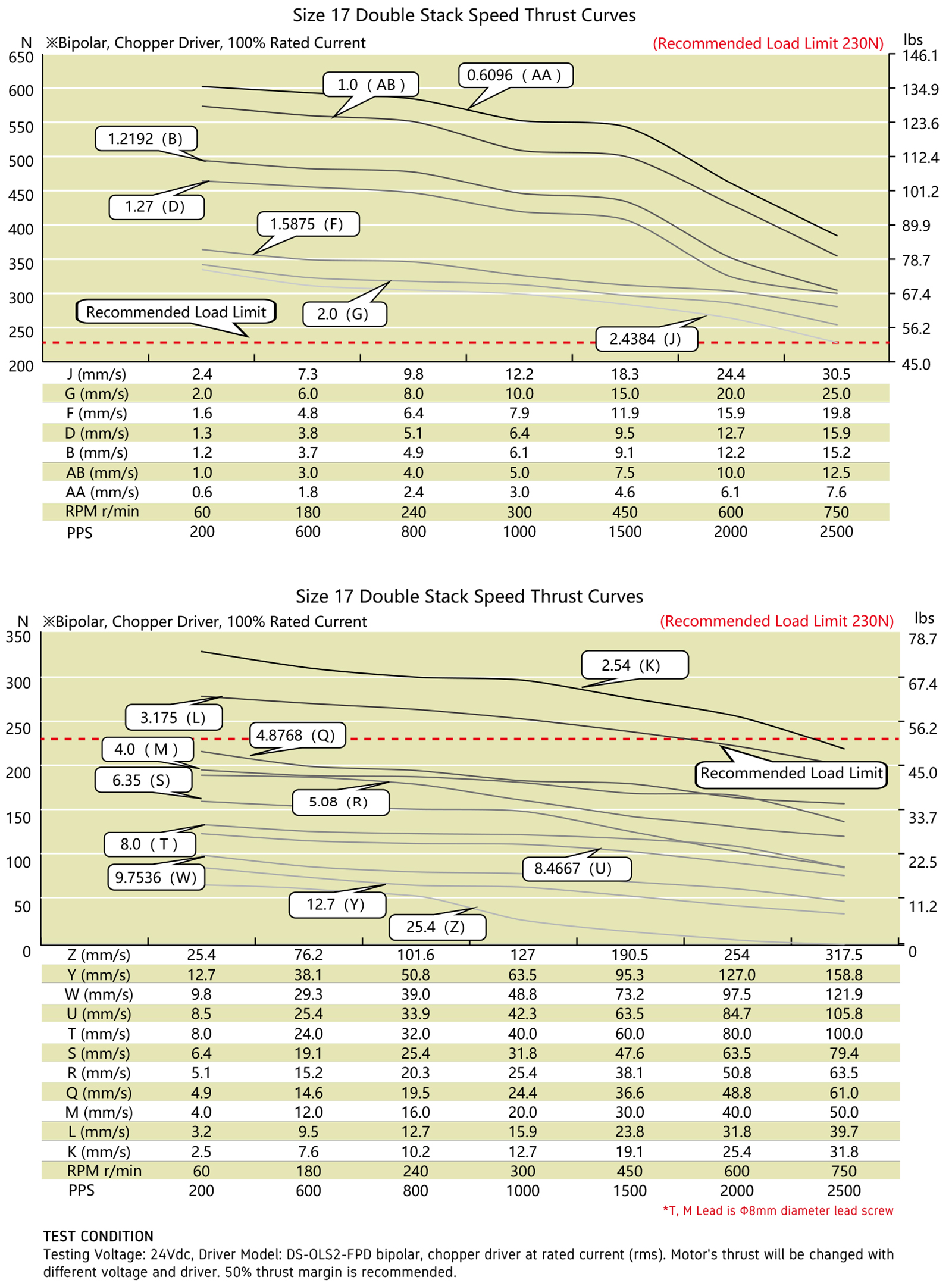
Options for screw end machining:
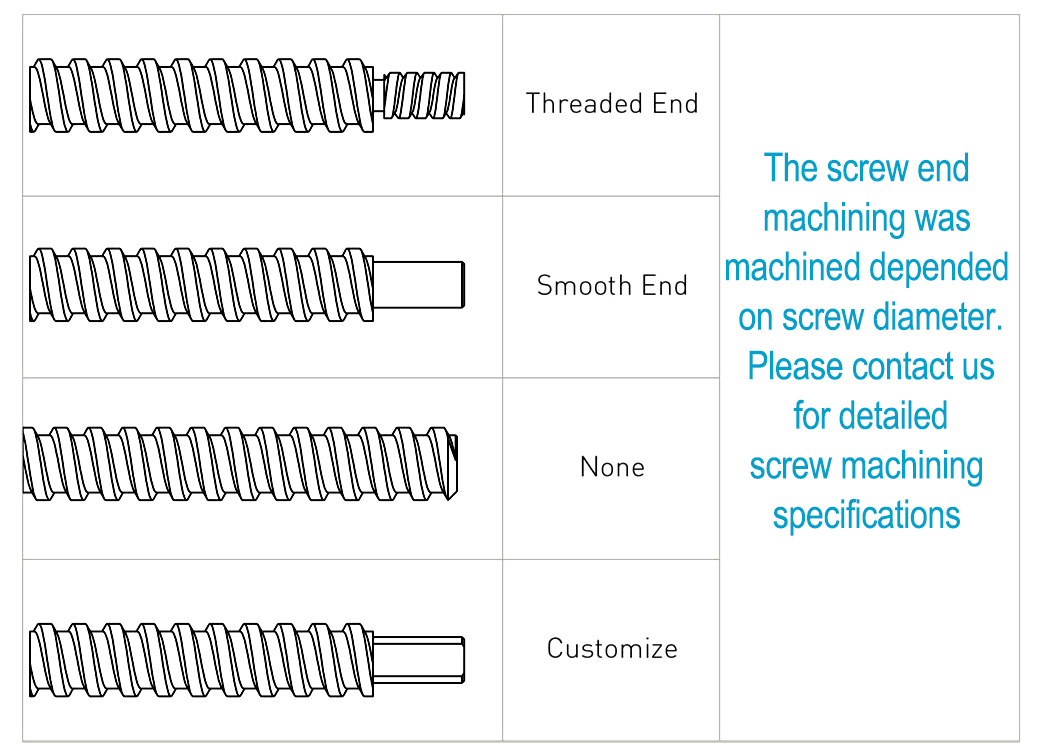
NEMA14 Stepper Lead Screw Linear Actuators
The NEMA 6 is our smallest hybrid linear actuators.
This compact unit can be integrated into various
Applications to provide precise linear positioning while
occupying less than 1 in2 of mounting footprint and
providing up to 44.5N of continuous thrust.
The Working Type for the Different Application Demand:
E: External Linear
N: Non-captive
C: Captive
K: Kaptive
Motor Characteristics:
Motor | Voltage[V] | Current[A] | Resistance[Ω] | Inductance[mH] | Weight[g] | Lead Wire No. | Motor Length[mm] |
---|---|---|---|---|---|---|---|
14-2105 | 6.6 | 0.5 | 13.2 | 14 | 189 | 4 | 33.6 |
14-2110 | 3.5 | 1 | 3.5 | 3.6 | 189 | 4 | 33.6 |
14-2115 | 2.7 | 1.5 | 1.8 | 1.9 | 189 | 4 | 33.6 |
14-2205 | 12 | 0.5 | 24 | 29 | 210 | 4 | 45.6 |
14-2210 | 6 | 1 | 6 | 7.2 | 210 | 4 | 45.6 |
14-2215 | 4 | 1.5 | 2.7 | 3.2 | 210 | 4 | 45.6 |
Available Lead Screw and Travel per Step:
Screw Dia.[inch] | Screw Dia.[mm] | Lead[inch] | Lead[mm] | Lead Code | Travel Per Step @ 1.8° [mm]* | Travel Per Step @ 0.9° [mm]* |
---|---|---|---|---|---|---|
0.25 | 6.35 | 0.024 | 0.6096 | AA | 0.003 | 0.0015 |
0.25 | 6.35 | 0.0394 | 1 | AB | 0.005 | 0.0025 |
0.25 | 6.35 | 0.048 | 1.2192 | B | 0.006 | 0.003 |
0.25 | 6.35 | 0.05 | 1.27 | D | 0.0064 | 0.0032 |
0.25 | 6.35 | 0.0625 | 1.5875 | F | 0.0079 | 0.004 |
0.25 | 6.35 | 0.096 | 2.4384 | J | 0.0122 | 0.0061 |
0.25 | 6.35 | 0.1 | 2.54 | K* | 0.0127 | 0.0064 |
0.25 | 6.35 | 0.125 | 3.175 | L* | 0.0159 | 0.0079 |
0.25 | 6.35 | 0.192 | 4.8768 | Q | 0.024 | 0.0122 |
0.375 | 6.35 | 0.2 | 5.08 | R* | 0.0254 | 0.0127 |
0.25 | 6.35 | 0.25 | 6.35 | S* | 0.0318 | 0.0159 |
0.25 | 6.35 | 0.3333 | 8.4667 | U | 0.0423 | 0.0212 |
0.25 | 6.35 | 0.384 | 9.7536 | W* | 0.0488 | 0.0244 |
0.25 | 6.35 | 0.5 | 12.7 | Y* | 0.0635 | 0.0318 |
0.25 | 6.35 | 1.0 | 25.4 | Z* | 0.127 | 0.0635 |
0.31 | 8 | 0.1575 | 4 | M | 0.02 | 0.01 |
0.31 | 8 | 0.315 | 8 | T | 0.04 | 0.02 |
0.31 | 8 | 0.0787 | 2 | G | 0.01 | 0.005 |
NEMA 14 Stepper Lead Screw Linear Actuators (External Type):
NEMA 14 Stepper Lead Screw Linear Actuators (Non-Captive Type):
NEMA 14 Stepper Lead Screw Linear Actuators (Captive Type):
Stroke Specification of Captive Actuactor:
Size A (mm) | Stroke B (mm) | L (mm) | |
---|---|---|---|
35.70 | 12.70 | Single Stack Motor 34.1 | Double Stack Motor 48.1 |
42.05 | 19.05 | ||
48.40 | 25.40 | ||
54.80 | 31.80 | ||
61.10 | 38.10 | ||
73.80 | 50.80 | ||
86.50 | 63.5 |
NEMA 14 Stepper Lead Screw Linear Actuators (Kaptive Type):
Stroke Specification of Kaptive Actuactor:
Size A (mm) | Stroke B (mm) | C (mm) | |
---|---|---|---|
L=34.1 | L=48.1 | ||
18.70 | 12.70 | 4.30 | 1.30 |
25.05 | 19.05 | 10.65 | 7.65 |
31.40 | 25.40 | 17.00 | 14.00 |
37.75 | 31.75 | 23.35 | 20.35 |
44.10 | 38.10 | 29.70 | 26.70 |
56.80 | 50.80 | 42.40 | 39.40 |
69.50 | 63.50 | 55.10 | 52.10 |
Speed Thrust Curves:
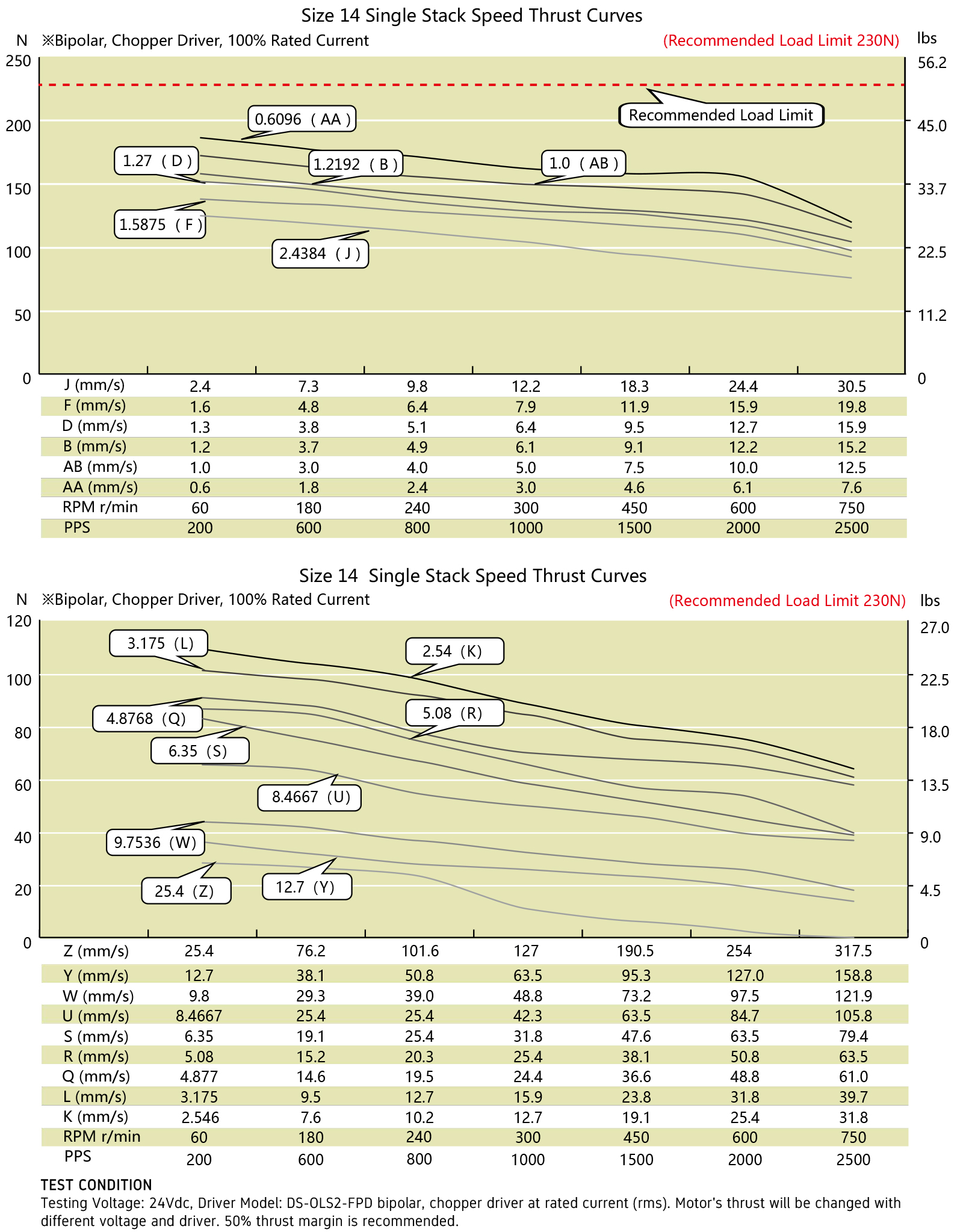
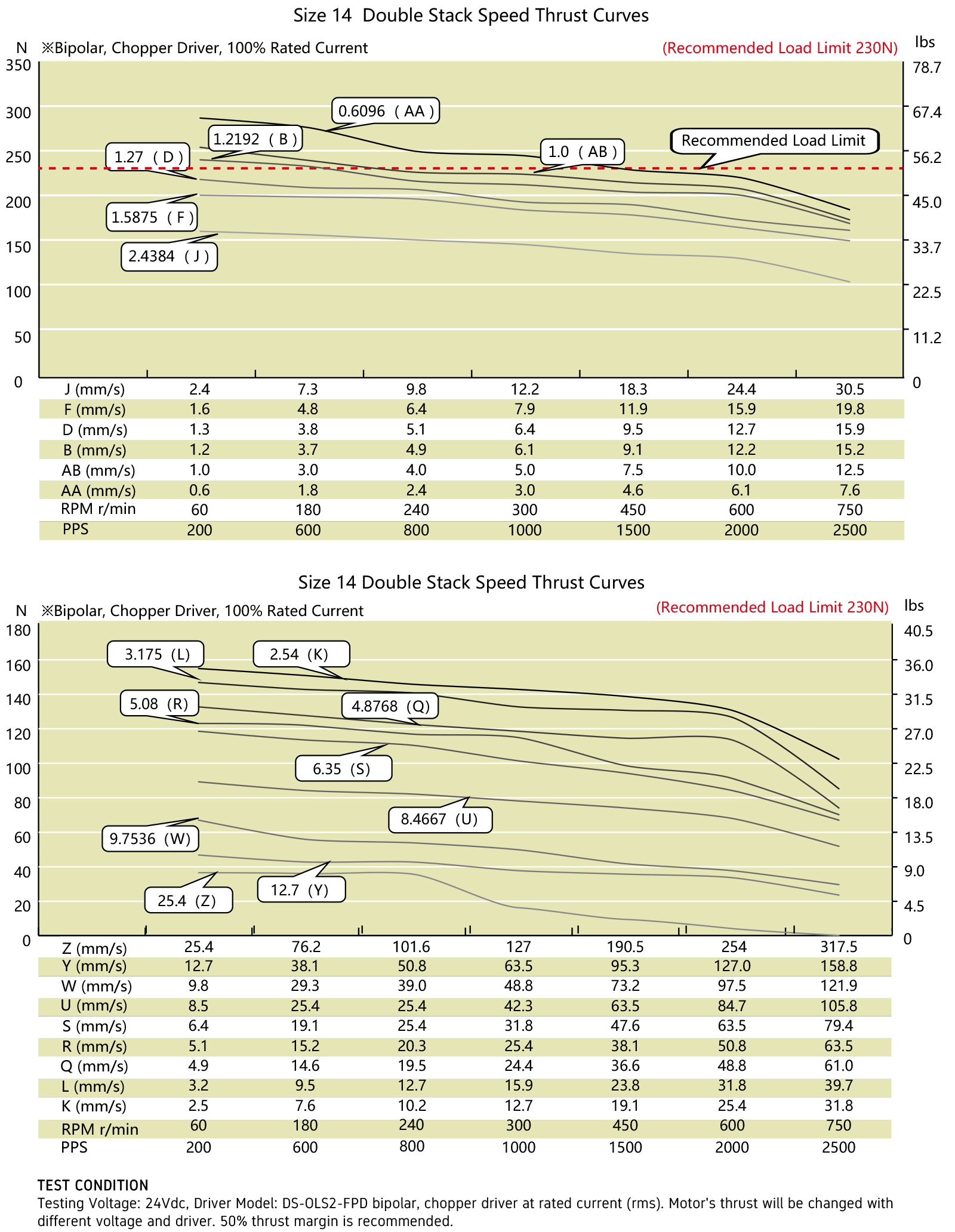
Options for screw end machining:
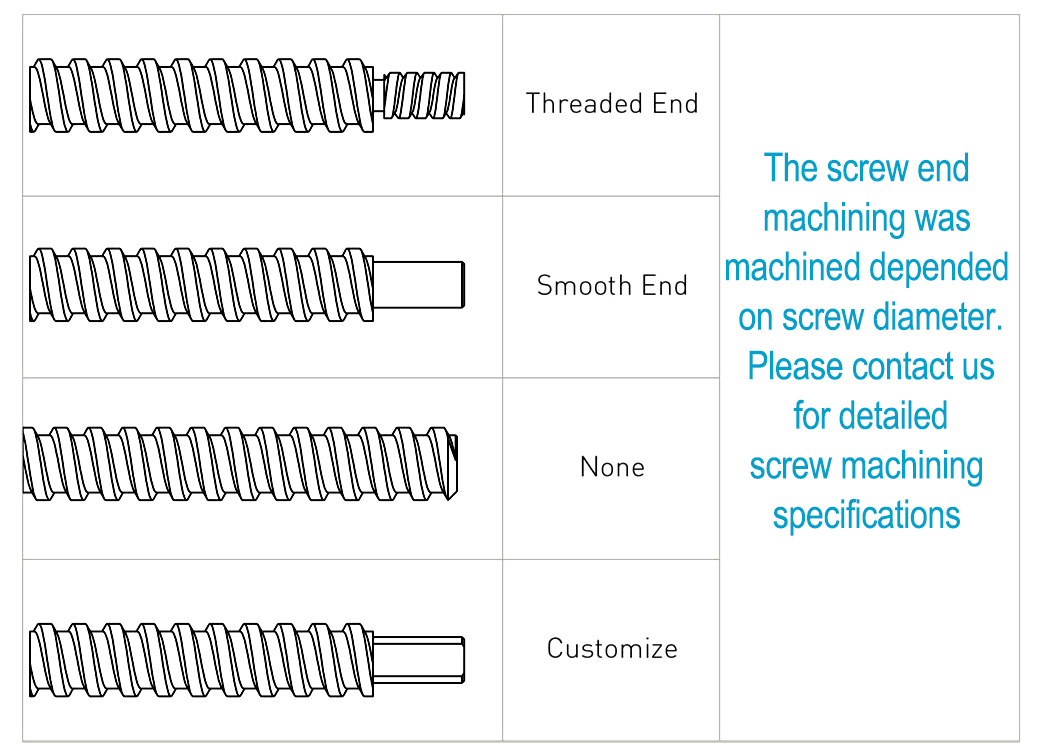
NEMA11 Stepper Lead Screw Linear Actuators
The NEMA 6 is our smallest hybrid linear actuators.
This compact unit can be integrated into various
Applications to provide precise linear positioning while
occupying less than 1 in2 of mounting footprint and
providing up to 44.5N of continuous thrust.
The Working Type for the Different Application Demand:
E: External Linear
N: Non-captive
C: Captive
K: Kaptive
Motor Characteristics:
Motor Code | Voltage (V) | Current (A) | Resistance (Ω) | Inductance (mH) | Weight (g) | Lead Wire No | Length (mm) |
11-2105 | 4.5 | 0.5 | 9.1 | 6 | 117 | 4 | 33.5 |
11-2110 | 2.2 | 1 | 2.1 | 1.2 | 117 | 4 | 33.5 |
11-2209 | 3.9 | 0.95 | 4.1 | 4 | 173 | 4 | 45 |
11-2216 | 2.25 | 1.6 | 1.45 | 1.1 | 173 | 4 | 45 |
Available Lead Screw and Travel per Step:
Screw Dia.[inch] | Screw Dia.[mm] | Lead[inch] | Lead[mm] | Lead Code | Travel Per Step @ 1.8° [mm]* |
---|---|---|---|---|---|
0.188 | 4.77 | 0.0125 | 0.3175 | AL | 0.0016 |
0.188 | 4.77 | 0.025 | 0.635 | A | 0.0032 |
0.188 | 4.77 | 0.05 | 1.27 | D | 0.0063 |
0.218 | 5.56 | 0.096 | 2.4384 | J* | 0.0122 |
0.188 | 4.77 | 0.1 | 2.54 | K | 0.0127 |
0.218 | 5.56 | 0.192 | 4.8768 | Q* | 0.0244 |
0.188 | 4.77 | 0.2 | 5.08 | R | 0.0254 |
0.188 | 4.77 | 0.4 | 10.16 | X | 0.0508 |
NEMA 11 Stepper Lead Screw Linear Actuators (External Type):
NEMA 11 Stepper Lead Screw Linear Actuators (Non-Captive Type):
NEMA 11 Stepper Lead Screw Linear Actuators (Captive Type):
Stroke Specification of Captive Actuactor:
Size A (mm) | Stoke B (mm) | L (mm) | |
---|---|---|---|
22.20 | 12.70 | Single Stack Motor 33.35 | Double Stack Motor 45 |
28.55 | 19.05 | ||
34.90 | 25.40 | ||
41.30 | 31.80 | ||
47.60 | 38.10 | ||
60.30 | 50.80 | ||
73.00 | 63.50 |
NEMA 11 Stepper Lead Screw Linear Actuators (Kaptive Type):
Stroke Specification of Kaptive Actuactor:
Size A (mm) | Stroke B (mm) | C (mm) | |
---|---|---|---|
L=33.35 | L=45 | ||
15.70 | 12.70 | 1.0 | 0.0 |
22.10 | 19.05 | 7.4 | 0.0 |
28.40 | 25.40 | 13.7 | 4.0 |
34.80 | 31.80 | 20.1 | 10.4 |
41.10 | 38.10 | 26.4 | 16.8 |
53.80 | 50.80 | 39.0 | 29.4 |
66.50 | 63.50 | 52.7 | 42.1 |
Speed Thrust Curves:
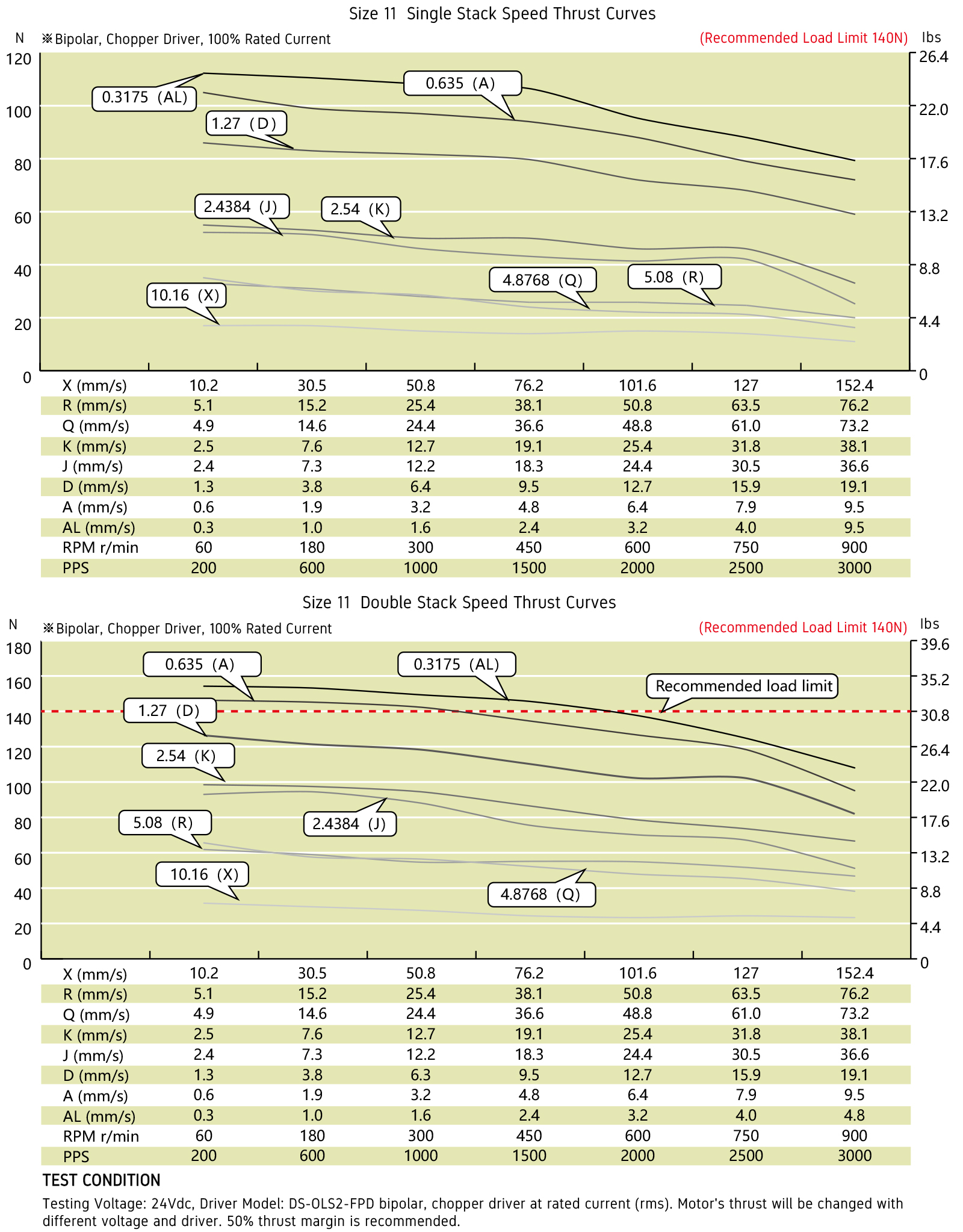
Options for screw end machining:
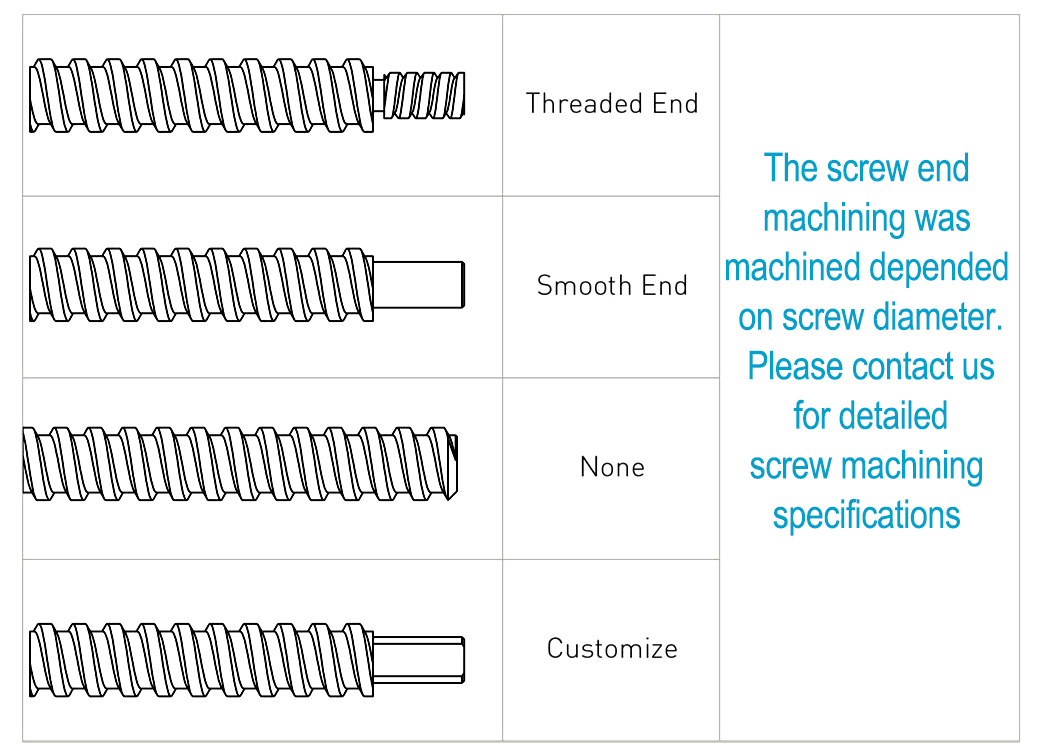
NEMA17 Stepper Ball Screw Linear Actuators
These actuators are external types have 5 different sizes, from 20mm to 57mm. From 0.005mm/
step to 0.1mm/step, variety of resolution for options available. Maximum thrust can reach 1600N.
Encoder option is available for whole Series
Motor size | NEMA8 | NEMA11 | NEMA14 | NEMA17 | NEMA23 | ||||
Dia. Lead | Φ4 | Φ5 | Φ6 | Φ6 | Φ8 | Φ6 | Φ8 | Φ10 | Φ12 |
1.0 mm | * | * | * | * | * | * | |||
2.0 mm | * | * | * | * | * | * | * | * | |
2.5 mm | * | * | |||||||
4.0 mm | * | * | |||||||
5.0 mm | * | * | * | ||||||
6.0 mm | * | * | * | ||||||
8.0 mm | * | * | |||||||
10.0 mm | * | * | * | * | * | * | * | ||
12.0 mm | * | * | |||||||
15.0 mm | * | ||||||||
20.0 mm | * |
NEMA17 Stepper Ball Screw Linear Actuators
Motor Characteristics:
Motor Code | Voltage (V) | Current (A) | Resistance (Ω) | Inductance (mH) | Lead Wire No | Length (mm) |
17E2105 | 7.2 | 0.5 | 14.4 | 19.8 | 4 | 34.1 |
17E2110 | 3.8 | 1.0 | 3.8 | 5.0 | 4 | 34.1 |
17E2115 | 2.78 | 1.5 | 1.85 | 2.2 | 4 | 48.1 |
17E2212 | 4.56 | 1.2 | 3.8 | 8.0 | 4 | 48.1 |
17E2225 | 2.25 | 2.5 | 0.9 | 1.8 | 4 | 48.1 |
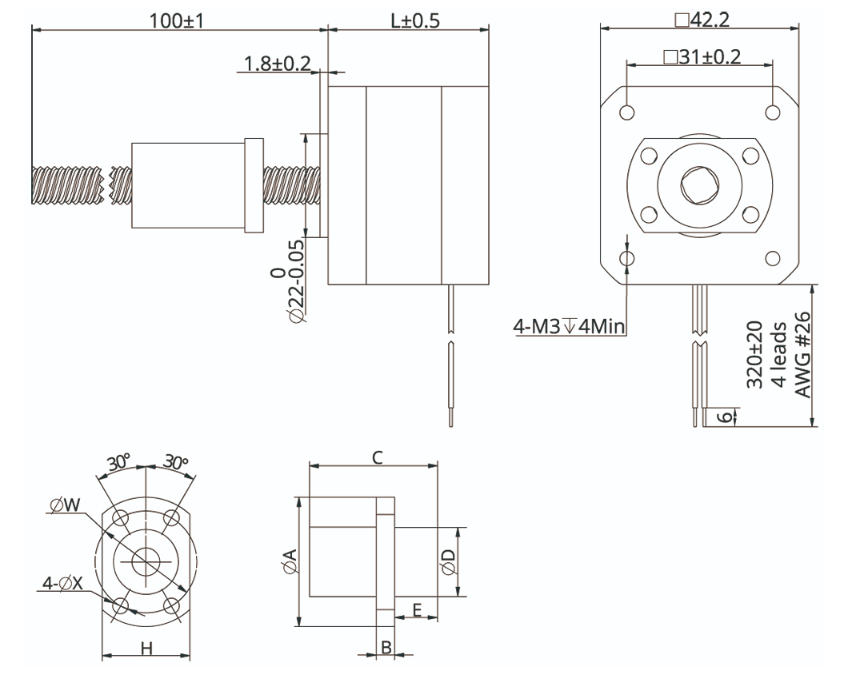
Ball screw type | 0801 | 0802 | 0802.5 | 0805 | 0808 | 0810 | 0812 |
---|---|---|---|---|---|---|---|
Ball Size | Ф0.8 | Ф1.5875 | Ф1.5875 | Ф1.5875 | Ф1.5875 | Ф1.5875 | Ф1.5875 |
Number of thread | 1 | 1 | 1 | 1 | 2 | 2 | 2 |
Thread direction | Right | ||||||
Shaft root dia. | Ф7.3 | Ф6.6 | Ф6.3 | Ф6.6 | Ф6.7 | Ф6.7 | Ф6.7 |
Number of circuit | 3.7×1 | 3.7×1 | 2.7×1 | 2.7×1 | 1.6×2 | 1.6×2 | 1.6×2 |
Shaft, nut material | SCM415H | ||||||
Surface hardness | HRC58~62 | ||||||
Anti-rust treatment | Anti-rust oil | ||||||
Grade | C7 |
Nut size | A | B | C | D | H | W | X | E | Position accuracy | Total run out | Axial play | Dynamic load[N] | Static load[N] |
---|---|---|---|---|---|---|---|---|---|---|---|---|---|
BS0801 | 29 | 4 | 17 | 16 | 18 | 23 | 3.4 | ±0.05 | 0.12 | ≤0.03 | 780 | 1650 | |
BS0802 | 37 | 5 | 24 | 20 | 22 | 29 | 4.5 | ±0.05 | 0.12 | ≤0.03 | 2400 | 4100 | |
BS0802.5 | 29 | 4 | 16 | 16 | 18 | 23 | 3.4 | ±0.05 | 0.12 | ≤0.03 | 1850 | 3000 | |
BS0805 | 31 | 4 | 28 | 18 | 20 | 25 | 3.4 | ±0.05 | 0.12 | ≤0.03 | 1850 | 3000 | |
BS0808 | 31 | 4 | 20 | 18 | 20 | 25 | 3.4 | 6 | ±0.05 | 0.12 | ≤0.03 | 2200 | 3800 |
BS0810 | 31 | 4 | 20 | 18 | 20 | 25 | 3.4 | 7 | ±0.05 | 0.12 | ≤0.03 | 2200 | 3800 |
BS0812 | 31 | 4 | 24 | 18 | 20 | 25 | 3.4 | 6 | ±0.05 | 0.12 | ≤0.03 | 2200 | 3800 |
* The unit of Position accuracy, Total run out and Axial play is [mm].
NEMA 17 Ball Screw Liner Stepper Motor Performance Curves:
Options for screw end machining:
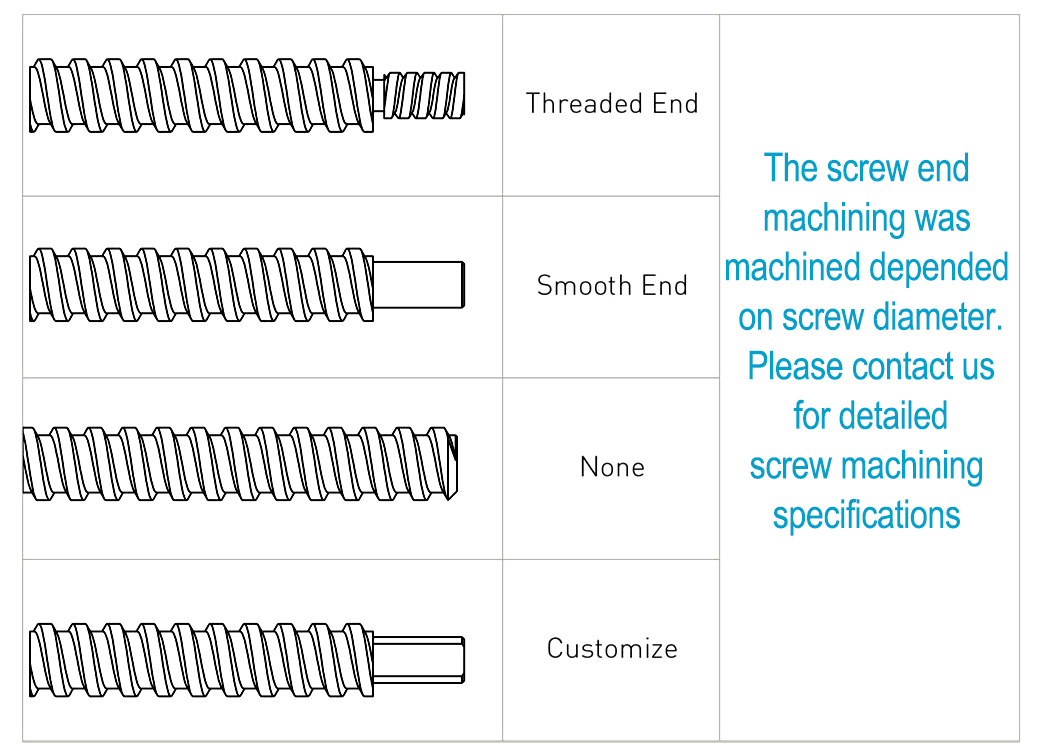
NEMA11 Stepper Ball Screw Linear Actuators
These actuators are external types have 5 different sizes, from 20mm to 57mm. From 0.005mm/
step to 0.1mm/step, variety of resolution for options available. Maximum thrust can reach 1600N.
Encoder option is available for whole Series
Motor size | NEMA8 | NEMA11 | NEMA14 | NEMA17 | NEMA23 | ||||
Dia. Lead | Φ4 | Φ5 | Φ6 | Φ6 | Φ8 | Φ6 | Φ8 | Φ10 | Φ12 |
1.0 mm | * | * | * | * | * | * | |||
2.0 mm | * | * | * | * | * | * | * | * | |
2.5 mm | * | * | |||||||
4.0 mm | * | * | |||||||
5.0 mm | * | * | * | ||||||
6.0 mm | * | * | * | ||||||
8.0 mm | * | * | |||||||
10.0 mm | * | * | * | * | * | * | * | ||
12.0 mm | * | * | |||||||
15.0 mm | * | ||||||||
20.0 mm | * |
NEMA11 Stepper Ball Screw Linear Actuators
Motor Characteristics:
Motor Code | Voltage (V) | Current (A) | Resistance (Ω) | Inductance (mH) | Lead Wire No | Length (mm) |
11E2105 | 4.55 | 0.5 | 9.1 | 4.8 | 4 | 33.5 |
11E2110 | 2.1 | 1.0 | 2.1 | 1.2 | 4 | 33.5 |
11E2209 | 3.9 | 0.95 | 4.1 | 4.0 | 4 | 45 |
11E2216 | 2.4 | 1.6 | 1.5 | 1.3 | 4 | 45 |
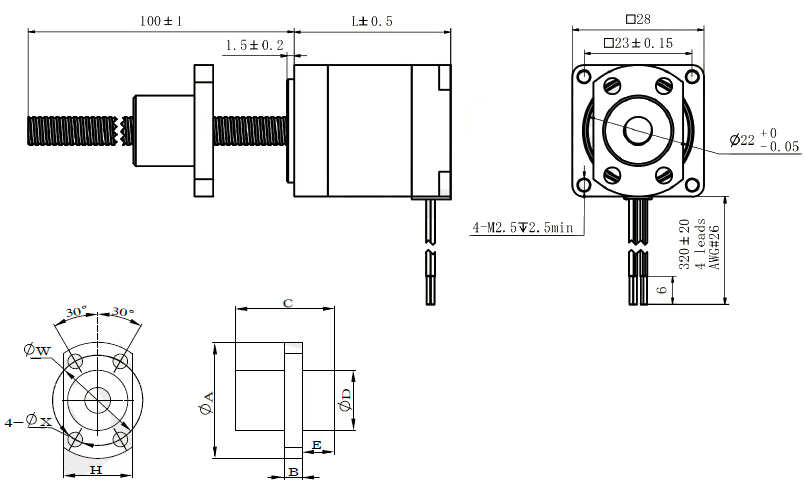
Ball screw type | SR0601 | SR0602 | SR0606 | SR0610 |
Ball Diameter | Ф0.8 | Ф0.8 | Ф0.8 | Ф0.8 |
Number of thread | 1 | 1 | ||
Thread direction | Right | Right | ||
Shaft root dia. | Ф5.3 | Ф5.1 | Ф5.2 | Ф5.0 |
Number of circuit | 3.7×1 | 2.7×1 | 1.6×1 | 1.2×2 |
Shat, nut material | SCM415H | SCM415H | ||
Surface hardness | HRC58~62 | HRC58~62 | ||
Anti-rust treatment | Anti-rust oil | Anti-rust oil |
Nut size | A | B | C | D | H | W | X | Grade | Position accuracy | Total run out | Axial play | Dynamic load(N) | Static load(N) |
SR0601 | 26 | 4 | 17 | 13 | 16 | 20 | 3.4 | C7 | Static | 0.12 | 0.02 | 680 | 1200 |
SR0402 | 26 | 4 | 17 | 15 | 19 | 22 | 3.4 | C7 | ±0.05 | 0.12 | 0.02 | 750 | 1450 |
SR0402 | 27 | 4 | 17 | 14 | 16 | 21 | 3.4 | C7 | ±0.05 | 0.12 | 0.02 | 870 | 1600 |
SR0402 | 27 | 4 | 17 | 14 | 16 | 21 | 3.4 | C7 | ±0.05 | 0.12 | 0.02 | 950 | 1650 |
NEMA 11 Ball Screw Liner Stepper Motor Performance Curves:
Options for screw end machining:
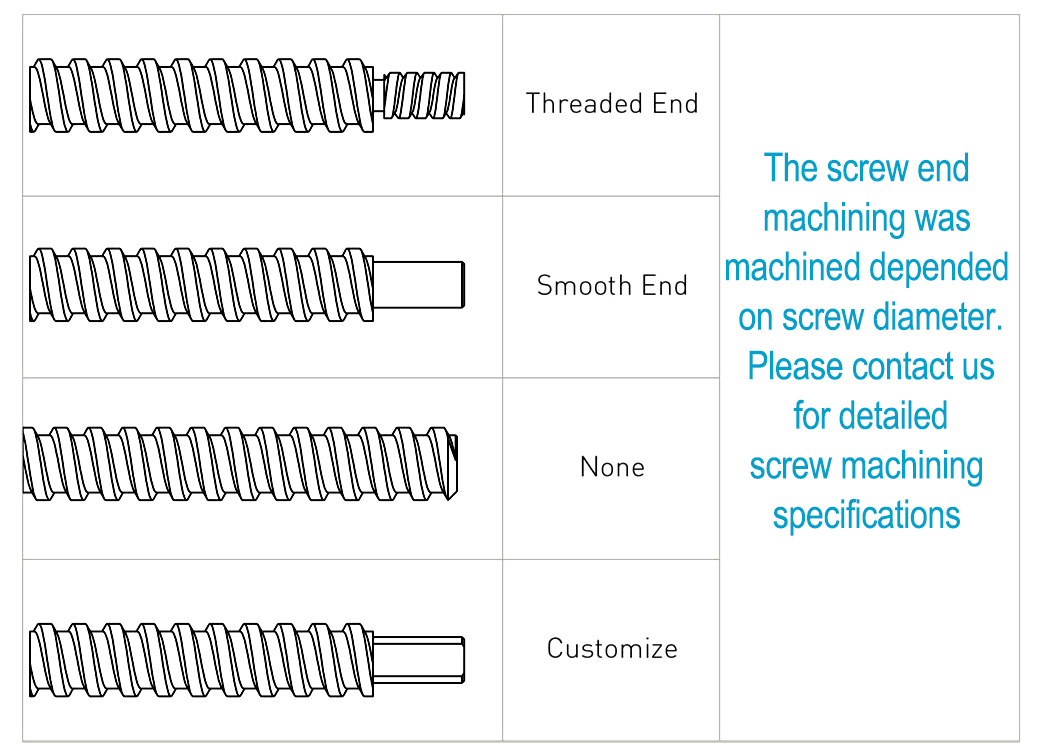
NEMA14 Stepper Ball Screw Linear Actuators
These actuators are external types have 5 different sizes, from 20mm to 57mm. From 0.005mm/
step to 0.1mm/step, variety of resolution for options available. Maximum thrust can reach 1600N.
Encoder option is available for whole Series
Motor size | NEMA8 | NEMA11 | NEMA14 | NEMA17 | NEMA23 | ||||
Dia. Lead | Φ4 | Φ5 | Φ6 | Φ6 | Φ8 | Φ6 | Φ8 | Φ10 | Φ12 |
1.0 mm | * | * | * | * | * | * | |||
2.0 mm | * | * | * | * | * | * | * | * | |
2.5 mm | * | * | |||||||
4.0 mm | * | * | |||||||
5.0 mm | * | * | * | ||||||
6.0 mm | * | * | * | ||||||
8.0 mm | * | * | |||||||
10.0 mm | * | * | * | * | * | * | * | ||
12.0 mm | * | * | |||||||
15.0 mm | * | ||||||||
20.0 mm | * |
NEMA14 Stepper Ball Screw Linear Actuators
Motor Characteristics:
Motor Code | Voltage (V) | Current (A) | Resistance (Ω) | Inductance (mH) | Lead Wire No | Length (mm) |
14E2105 | 6.6 | 0.5 | 13.2 | 14 | 4 | 33.6 |
14E2110 | 3.5 | 1.0 | 3.5 | 3.6 | 4 | 33.6 |
14E2115 | 2.7 | 1.5 | 1.8 | 1.9 | 4 | 45.6 |
14E2205 | 12 | 0.5 | 24 | 29 | 4 | 45.6 |
14E2210 | 6 | 1.0 | 6 | 7.2 | 4 | 45.6 |
14E2215 | 4 | 1.5 | 2.7 | 3.2 | 4 | 45.6 |
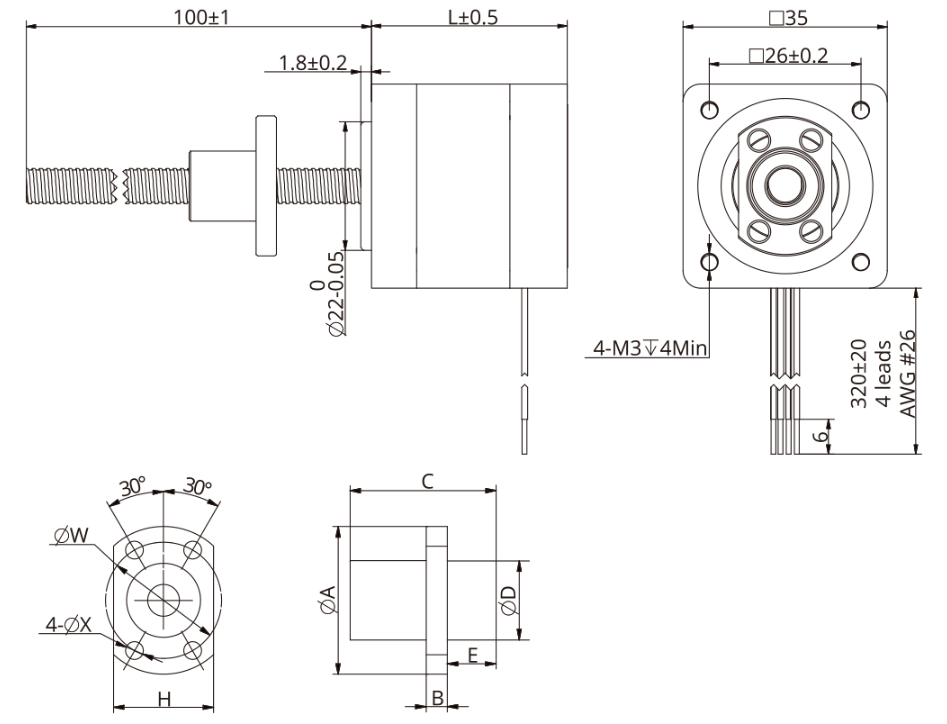
Ball screw type | 0601 | 0602 | 0606 | 0610 | 0801 | 0802 | 0802.5 | 0805 | 0808 | 0810 | 0812 |
---|---|---|---|---|---|---|---|---|---|---|---|
Ball Size | Ф0.8 | Ф0.8 | Ф0.8 | Ф1.2 | Ф0.8 | Ф1.5875 | Ф1.5875 | Ф1.5875 | Ф1.5875 | Ф1.5875 | Ф1.5875 |
Number of thread | 1 | 1 | 2 | 2 | 1 | 1 | 1 | 1 | 2 | 2 | 2 |
Thread direction | Right | ||||||||||
Shaft root dia. | Ф5.3 | Ф5.1 | Ф5.2 | Ф5.0 | Ф7.3 | Ф6.6 | Ф6.3 | Ф6.6 | Ф6.7 | Ф6.7 | Ф6.7 |
Number of circuit | 3.7×1 | 2.7×1 | 1.6×2 | 1.2×2 | 3.7×1 | 3.7×1 | 2.7×1 | 2.7×1 | 1.6×2 | 1.6×2 | 1.6×2 |
Shaft, nut material | SCM415H | ||||||||||
Surface hardness | HRC58~62 | ||||||||||
Anti-rust treatment | Anti-rust oil | ||||||||||
Grade | C7 |
Nut size | A | B | C | D | H | W | X | E | Position accuracy | Total run out | Axial play | Dynamic load[N] | Static load[N] |
---|---|---|---|---|---|---|---|---|---|---|---|---|---|
BS0601 | 26 | 4 | 17 | 13 | 16 | 20 | 3.4 | ±0.05 | 0.12 | ≤0.03 | 680 | 1200 | |
BS0602 | 28 | 4 | 17 | 15 | 19 | 22 | 3.4 | ±0.05 | 0.12 | ≤0.03 | 750 | 1450 | |
BS0606 | 27 | 4 | 17 | 14 | 16 | 21 | 3.4 | 5 | ±0.05 | 0.12 | ≤0.03 | 870 | 1600 |
BS0610 | 27 | 4 | 23 | 14 | 16 | 21 | 3.4 | 7.5 | ±0.05 | 0.12 | ≤0.03 | 950 | 1650 |
BS0801 | 29 | 4 | 17 | 16 | 18 | 23 | 3.4 | ±0.05 | 0.12 | ≤0.03 | 780 | 1650 | |
BS0802 | 37 | 5 | 24 | 20 | 22 | 29 | 4.5 | ±0.05 | 0.12 | ≤0.03 | 2400 | 4100 | |
BS0802.5 | 29 | 4 | 16 | 16 | 18 | 23 | 3.4 | ±0.05 | 0.12 | ≤0.03 | 1850 | 3000 | |
BS0805 | 31 | 4 | 28 | 18 | 20 | 25 | 3.4 | ±0.05 | 0.12 | ≤0.03 | 1850 | 3000 | |
BS0808 | 31 | 4 | 20 | 18 | 20 | 25 | 3.4 | 6 | ±0.05 | 0.12 | ≤0.03 | 2200 | 3800 |
BS0810 | 31 | 4 | 20 | 18 | 20 | 25 | 3.4 | 7 | ±0.05 | 0.12 | ≤0.03 | 2200 | 3800 |
BS0812 | 31 | 4 | 24 | 18 | 20 | 25 | 3.4 | 6 | ±0.05 | 0.12 | ≤0.03 | 2200 | 3800 |
* The unit of Position accuracy, Total run out and Axial play is [mm].
NEMA 14 Ball Screw Liner Stepper Motor Performance Curves:
Options for screw end machining:
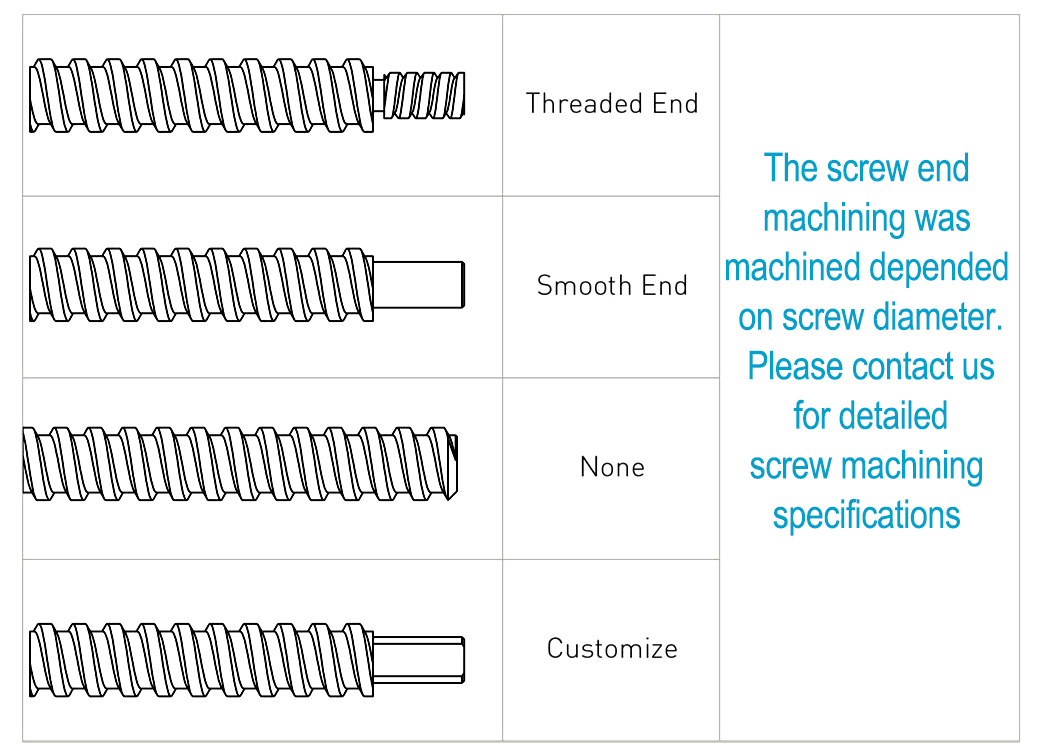
magnitude and phase of inverter AC voltage, so as to achieve the purpose of reactive power compensation and 3 phase load balancing .
Because the switching frequency of IGBT is very high (up to 25.6kHz), SVG can compensate rapid reactive loads and achieve quite high
compensation accuracy. SVG is the best product in the field of reactive power control.
Static Var Generator detects load current in real time through internal and external CT and analyzes the reactive current of load by TI DSP and FPGA,
then generates PWM signal to IGBT inverter(3 Level) to generate inductive or capacitive current and compensate reactive current to realize the target power factor.
SVG can also compensate phase imbalance. Compared with the traditional capacitor bank, SVG has the advantages of fast response and high compensation accuracy
without under-compensation or over-compensation problems, avoid resonance,etc.
Modular Design:
Model Description:
SN | Item | Rated Capacity | Model No. | Dimensions (W*D*H,MM) | N.W (KG) | Packing Size (W*D*H,MM) | G.W. (KG) |
1 | SVG | 10kVAr | SVG/10 | 360*402*125 | 20 | 740*690*445 | 25 |
2 | SVG | 15kVAr | SVG/15 | 360*402*125 | 20 | 740*690*445 | 25 |
3 | SVG | 30kVAr | SVG/30 | 505*550*190 | 34 | 740*690*445 | 40 |
4 | SVG | 50kVAr | SVG/50 | 505*550*190 | 35 | 740*690*445 | 41 |
5 | SVG | 75kVAr | SVG/75 | 505*570*280 | 50 | 740*690*445 | 63 |
6 | SVG | 85kVAr | SVG/85 | 505*570*280 | 53 | 740*690*445 | 64 |
7 | SVG | 100kVAr | SVG/100 | 505*570*280 | 55 | 740*690*445 | 65 |
ADVANTAGES:
Static Var Generators are high performance, compact, flexible, modular and cost-effective Active Power Factor Correction systems
that provide an instantaneous and effective response to power quality problems in low or high voltage electric power systems.
Connected in parallel with the load to be compensated, SVG units act as a controlled current source, providing a current waveform in real time.
- Three level topology
- Ultra-compact Modular design
- Fastest switching frequency 25.6kHz
- Lowest power consumption ≤ 2.5%
- Leading dissipation technology
- Continuous power factor correction
- Precise PF maintain -1.0 ≤ CosΦ ≤ 1.0
- Both capacitive and inductive control
- No over or under-compensation
- Hybrid power factor correction
- Saving Electricity Bills
- Energy saving
- 3 phase load balancing
- Low noise
- Friendly Human Machine Interfac
- TI DSP, Infineon or Semikron IGBT
- High Stability,avoids resonance
- Both Hardware and software protection
- High Reliability Test
- Good Environmental adaptability
Static Var Generator enable longer equipment lifetime, higher process reliability, improved power system capacity and stability,
and reduced energy losses, complying with most demanding power quality standards and grid codes.
Technical Data and Specifications | ||||
Rated Voltage | 220V (171~269V) | 400V (300~456V) | 480V (356~515V) | 690V (483~793V) |
Rated Current | 10/20/30/40/50kVAr | 30/50/75/100kVAr | 30/50/75/100kVAr | 150/175/200kVAr |
Mains Frequency | 50/60Hz±5% | |||
Circuit Topology | Three Level | |||
Multi Compensation Mode | Reactive compensation, three-phase load unbalance compensation | |||
Target Power Factor | Adjustable from -1.0 to 1.0 | |||
3 Phase Load Balancing Effect | ≤5%, Mitigate negative and zero sequence | |||
Switching/control frequency | 25.6kHz | |||
Initial response time | ≤50us | |||
Overall Response time | ≤5ms | |||
Active loss of system | ≤2.5% | |||
Output current limit | Automatically limited within 100% of rated capacity to output | |||
Control algorithm | Intelligent FFT,Self-adaptive control algorithm | |||
Controller | DSP FPGA | |||
Protection | Hardware protection, Software protection | |||
Control connection | Fiber or electrical connection | |||
Human Machine Interface | 7 inch touched TFT LCD HMI | |||
Communication protocols | Adopt Modbus remote communication protocol; communication interface adopts RS485 and CAN bus, supporting mobile phone APP operation. | |||
Noise | <60db (<45db during low-speed operation) | |||
Installation method | Module embedded(Rack),wall mounted, free landing | |||
Level of protection | IP20 | |||
Cooling method | Speed regulation intelligent air cooling PWM Fans | |||
Color | RAL 7035 Light Grey | |||
Ambient temperature | -20~55℃ | |||
Relative humidity | Maximum 95%, without condensation | |||
Mounting height above sea level | ≤2000 at rated capacity; appropriately reduce the capacity if it is > 2000(1% derating per 100m) | |||
Qaulifications | CE, IEEE61000,Type Test Report | |||
Compliance with Standards | IEEE 519, ERG5/4 |
APPLICATIONS:
Oil drilling industry leads to a large number of reactive power consumption, resulting in poor stability of the power system.
AC-DC conversion during the operation of DC electric drive drilling rig will produce a large amount of harmonic wave components,
which causes serious pollution to the power supply system. Meanwhile, the harmonic pollution makes drilling system usually run
with power factor under 0.5, and generators cannot be fully utilized, which increases the investment of equipment and energy consumption.
The method of quickly and effectively compensating reactive load of mine power network is in urgent need...
After installed Static Var Generator, the site data compliance with IEEE 519, G5/4, EN 50160 and also other power quality
standards and recommendations
- Energy savings
- Higher productivity
- Reliable plant operation at reduced maintenance costs
- Additional electric capacity in existing electrical network
- Quick return on investment
Technical Performance:
such as harmonics, reactive power and 3 phase load unbalance. which is in parallel to power grid can
detect the harmonic wave in power grid in time,generate the reverse-phase compensation current
through the converter and dynamically filter the harmonic wave in power grid.
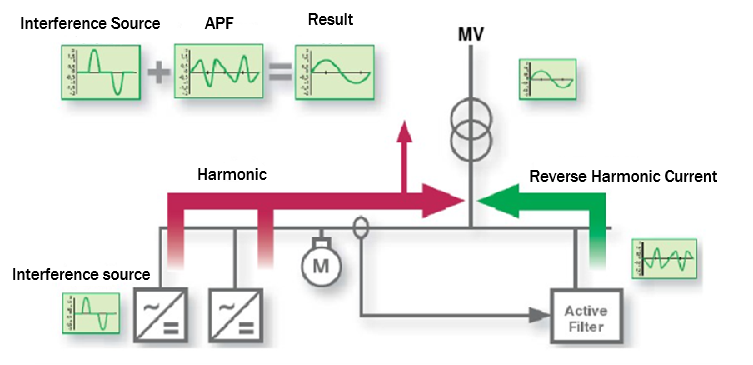
The operation of APF is unaffected by multifarious load forms and power grid structures.
And it will not produce harmonic oscillation (resonance) along with the system, thus perfectly
realizing harmonic control under diverse loads. Active Power Filter can fully accomplish dynamic
reactive compensation, control the capacitor switching and ultimately heighten the power factor
of power grid. Meanwhile, APF has the function of controlling the three-phase load current unbalance,
thus comprehensively handling various power quality matters in power grid.
Modular Design:
Model Description:
SN | Item | Rated Capacity | Model No. | Dimensions (W*D*H,MM) | N.W (KG) | Packing Size (W*D*H,MM) | G.W. (KG) |
1 | APF | 15A | APF/15 | 450 x 515 x 160 | 20 | 740*690*445 | 25 |
2 | APF | 25A | APF/25 | 450 x 515 x 160 | 25 | 740*690*445 | 30 |
3 | APF | 50A | APF/50 | 450 x 515 x 160 | 34 | 740*690*445 | 40 |
4 | APF | 75A | APF/75 | 450 x 515 x 160 | 35 | 740*690*445 | 40 |
5 | APF | 100A | APF/100 | 505 x 616 x 220 | 50 | 740*690*445 | 63 |
6 | APF | 125A | APF/125 | 505 x 616 x 220 | 53 | 740*690*445 | 64 |
7 | APF | 150A | APF/150 | 505 x 616 x 220 | 55 | 740*690*445 | 65 |
Advantages:
Active Power Filter is a modular, flexible, high-efficiency power quality solution for modern power networks’ problems,
such as harmonics, low power factor and unbalances and so on.
APF protects critical industrial, residential and commercial applications, solving tough power quality problems for all type
of applications and customers globally.
- Three level topology
- Ultra-compact Modular design
- Fastest switching frequency 25.6kHz
- Lowest power consumption ≤ 2.5%
- Leading dissipation technology
- Self-adaptive algorithm(ADALINE)
- THDi less than 5% at rated load
- High filtering efficiency up to 98%
- Fast Response time less than 5ms
- Selective or Full compensation
- Continuous power factor correction
- Both capacitive and inductive control
- Precise PF maintain -1.0 ≤ CosΦ ≤ 1.0
- 3 phase load balance less than 5%
- Mitigates neutral current
- TI DSP, Infineon or Semikron IGBT
- High Stability,avoids resonance
- Both Hardware and software protection
- High Reliability Test
- Good Environmental adaptability
Active Power Filter is available in a wide range of ratings, to serve a wide range of consumer applications. Its modular design
allows flexibility in installation and integration. The inherent energy-efficient design,3 level topology, and the optional
user-friendly Haman Machine Interface, make APF a highly preferred solution for all segments of electricity consumers,
system integrators and OEM manufacturer.
Technical Data and Specifications | ||||
Rated Voltage | 220V (171~269V) | 400V (300~456V) | 480V (356~515V) | 690V (483~793V) |
Rated Current | 15/25/50/75/100/150A | 15/25/50/75/100/150A | 50/75A/100/120A | 100A,150A |
Mains Frequency | 50/60Hz±5% | |||
Circuit Topology | Three Level | |||
Multi Compensation Mode | Harmonic compensation, reactive compensation, three-phase load unbalance compensation | |||
Filter range | 2nd~51st odd order harmonics (Selective or Full compensation) | |||
Rated of Harmonic Reduction | ≥97% (For typical harmonic order distortions) | |||
Filtering Performance | Typically, THDi≤ 5% at rated load(Even with most complex loads). | |||
Target Power Factor | Adjustable from -1.0 to 1.0 | |||
3 Phase Load Balancing Effect | ≤5%, Mitigate negative and zero sequence | |||
Neatral Filtering Capacity | 3 times the rated filter current(in case of 4 wire device) | |||
Switching/control frequency | 25.6kHz | |||
Initial response time | ≤50us | |||
Overall Response time | ≤5ms | |||
Active loss of system | ≤2.5% | |||
Output current limit | Automatically limited within 100% of rated capacity to output | |||
Control algorithm | Intelligent FFT,Self-adaptive control algorithm | |||
Controller | DSP FPGA | |||
Protection | Hardware protection, Software protection | |||
Control connection | Fiber or electrical connection | |||
Human Machine Interface | 7 inch touched TFT LCD HMI | |||
Communication protocols | Adopt Modbus remote communication protocol; communication interface adopts RS485 and CAN bus, supporting mobile phone APP operation. | |||
Noise | <60db (<45db during low-speed operation) | |||
Installation method | Module embedded(Rack),wall mounted, free landing | |||
Level of protection | IP20 | |||
Cooling method | Speed regulation intelligent air cooling PWM Fans | |||
Color | RAL 7035 Light Grey | |||
Ambient temperature | -20~55℃ | |||
Relative humidity | Maximum 95%, without condensation | |||
Mounting height above sea level | ≤2000 at rated capacity; appropriately reduce the capacity if it is > 2000(1% derating per 100m) | |||
Qaulifications | CE, IEEE61000,Type Test Report | |||
Compliance with Standards | IEEE 519, ERG5/4 |
APPLICATIONS:
Active Power Filter reduced harmonic levels results in improved electrical network reliability and reduced operating costs. Nuisance tripping
of protective devices and nuisance clearing of fuses due to harmonic heating effects is greatly reduced.
Overheating of motors, transformers, switchgear and cables is also reduced which increases their life expectancy and reduces maintenance costs.
For new installations, over-sizing of distribution equipment to reduce harmonic susceptibility can be reconsidered.
With the development of social economy and science technology, many textile printing and dyeing enterprises in order to improve the product quality
of transformation technology, large use of VFDs, DC equipment, including ventilation equipment (including frequency conversion fan and air conditioning),
lighting equipment, production equipment (yarn, fine sand, grasp cotton, shaping machine, dyeing cylinder, etc.), produce a large number of 5th,7th order harmonic,
cause harmonic, harmonic pollution, lead to power quality decline.
Adampower is specialized in the production of non-woven fabric manufacturer, producing a variety
of short fiber non-woven cloth, varieties of melt-blown non-woven cloth, synthetic leather non-woven cloth,
acupuncture non-woven cloth, propylene non-woven cloth, water absorption pad, filter non-woven cloth,
antibacterial cotton, automotive interior materials, oil absorption mat and other non-woven products
The industrial load mainly includes carding machine, needle acupuncture machine, non-woven oven, coil machine, etc.
which will produce series harmonics in the production process, resulting in the field capacitance compensation cabinet
can not work normally.In order to ensure the normal operation of the field capacitors cabinet,
the 300A active power filter is installed for harmonic mitigation.
Will compliance with IEEE 519, G5/4, EN 50160 and also other power quality standards and recommendations:
- Energy savings
- Higher productivity
- Quick return on investment
- Longer lifetime of electrical and process equipment
- Reliable operation at reduced maintenance costs
- Additional electric capacity in existing power grid
Grid Data show the difference:
However, they are one of the major sources of harmonic distortions in the network. APF Active Power Filters can effectively cancel the harmonic
distortions created by variable speed drives in industrial applications. APF bring power quality benefits to variety of industries including the following,
Step Accuracy: | ±5% | Resistance Accuracy: | ±10% |
---|---|---|---|
Inductance Accuracy: | ±20% | Temperature Rise: | 80°C MAX |
Ambient Temperature Range: | -20°C~ 50°C | Storage Temperature Range: | -30°C~ 60°C |
Insulation Resistance: | 100M Ω MIN. 500V DC | Dielectric Strength: | 500V AC 1min |
Radial Play: | 0.02mm MAX. (450g Load) | End Play: | 0.08mm MAX. (450g Load) |
Max. Radial Force: | 20N | Max. Axial Force: | 2N |
NEMA34 Stepper Motor, Closed Loop stepper motor
Electrical Specifications:
Mode No. | Step Angle | Motor Length mm | Rated Current A | Holding Torque (MIN) N.m | Motor Weight kg | Shaft Dia. mm |
34K280-02ED1000 | 1.8 | 95.8 | 3.0 | 4.5 | 2.1 | 14 |
34K280-03ED1000 | 1.8 | 95.8 | 4.5 | 4.5 | 2.1 | 14 |
34K280-04ED1000 | 1.8 | 95.8 | 6.0 | 4.5 | 2.1 | 14 |
34K2120-02ED1000 | 1.8 | 134.1 | 3.0 | 8.5 | 3.6 | 14 |
34K2120-03ED1000 | 1.8 | 134.1 | 4.5 | 8.5 | 3.6 | 14 |
34K2120-04ED1000 | 1.8 | 134.1 | 6.0 | 8.5 | 3.6 | 14 |
Stepper motor with 1000 Line Encoder:
1. Black : EGED
2. RED : 5VCC
3. Blue/White : EA-
4 Blue : EA
5. Orange/White : EB-
6. Orange : EB
Mechanical Dimensions and Wiring Diagram:
NEMA34 Stepper Motor with encoder, 34K280ED1000
DC60V Torque Speed Curve:
NEMA34 Stepper Motor with encoder, 34K2120ED1000:
DC60V Torque Speed Curve:
Lead Wire Mode Options:
Shaft Mode can be customized as the requirement.